as shown to eliminate possible errors. In reassembly,
refer first to the sets of punchmarks to determine the
approximate position of the parts. Then line up the
scribed lines to determine the exact position.
To make the intersection of two layout lines, bring
the point of the prick punch to the exact point of
intersection and tap the punch lightly with a hammer.
If inspection shows that the exact intersection and the
punchmark do not coincide, as in view A of figure
1-37, slant the punch as shown in view B and strike
again with the hammer, thus enlarging the punchmark
and centering it exactly. When the intersection has
been correctly punched, finish off with a light blow on
the punch held in an upright position. View C shows
the corrected punchmark.
DRIFT punches, sometimes called starting
punches, have a long taper from the tip to the body.
They are made that way to withstand the shock of
heavy blows. They may be used for knocking out
rivets after the heads have been chiseled off or for
freeing pins that are frozen in their holes.
After a pin has been loosened or partially driven
out, the drift punch may be too large to finish the job.
The follow-up tool to use is the PIN PUNCH. It is
designed to follow through the hole without jamming.
Always use the largest drift or pin punch that will tit
the hole. These punches usually come in sets of three
to five assorted sizes. Both of these punches will
have flat ends, never edged or rounded.
Figure 1-37.-Marking the intersection of lines with a prick
To remove a bolt or pin that is extremely tight,
start with a drift punch that has an end diameter that
is slightly smaller than the diameter of the object you
are removing. As soon as the bolt or pin loosens,
finish driving it out with a pin punch. Never use a
pin punch for starting a pin, because it has a slim
shank and a hard blow may cause it to bend or break.
For assembling units of a machine, an
ALIGNMENT (aligning) punch is invaluable. It is
usually about 1-foot long and has a long gradual taper.
Its purpose is to line up holes in mating parts.
Hollow metal-cutting punches are made from
hardened tool steel. They are made in various sizes
and are used to cut holes in light gauge sheet metal.
Other punches have been designed for special
uses. One of these is the soft-faced drift. It is made
of brass or fiber and is used for such jobs as removing
shafts, bearings, and wrist pins from engines. It is
generally heavy enough to resist damage to itself, but
soft enough not to injure the finished surface on the
part that is being driven.
You may have to make gaskets of rubber, cork,
leather, or composition materials. For cutting holes in
gasket materials, a hollow shank GASKET PUNCH
may be used (fig. 1-35). Gasket punches come in sets
of various sizes to accommodate standard bolts and
studs. The cutting end is tapered to a sharp edge to
produce a clean uniform hole. To use the gasket
punch, place the gasket material to be cut on a piece
of hard wood or lead so that the cutting edge of the
punch will not be damaged. Then strike the punch
with a hammer, driving it through the gasket where
holes are required.
TAPS AND DIES
Taps and dies are used to cut threads in metal,
plastics, or hard rubber. The taps are used for cutting
internal threads, and the dies are used to cut external
threads.
There are many different types of taps.
However, the most common are the taper, plug,
bottoming, and pipe taps (fig. 1-38).
The taper (starting) hand tap has a chamfer length
of 8 to 10 threads. These taps are used when starting
a tapping operation and when tapping through holes.
1-23
punch.
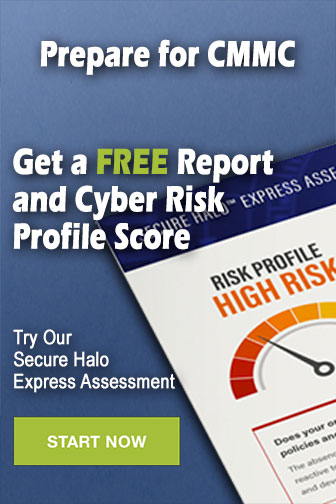