to 17 minutes the temperature increases gradually
until it reaches 120° to 135°F. Then a sudden, sharp
increase in temperature occurs until it reaches its peak
at or about 350°F. This sudden, sharp rise in tempera-
ture is known as kick-over. At this temperature, the
resin-hardener mixture begins to solidify and change
color from gray to light brown. The peak temperature
(350°F) can be observed through the external change
of the patch.
The resin-hardener mixture begins to cool slowly
because the materials conduct heat poorly. After kick-
over, the mixture continues to harden and increase in
strength. This process is called curing. Approximately
30 minutes after kick-over (the sharp rise in tempera-
ture), the patch is strong and hard and cool enough to
use. Pressure should not be restored to the system
until the patch has cured. The patch is considered
sufficiently cured when the bare hand can be placed
on it without discomfort from heat.
Several factors contribute to the control of kick-
over. The most important factor is the temperature.
Both the initial temperature of the activated resin
mixture and the temperature of the atmosphere affect
the kick-over time. Of these two temperatures, the
initial temperature of the activated resin has the
greater effect. When the temperature of the resin and
the hardener before mixing is increased, the kickover
time decreases. Conversely, when the temperature of
the resin and hardener before mixing decreases, the
kick-over time increases.
A knowledge of the control of kick-over is neces-
sary since it corresponds to the application of working
time. This means, for example, that when the initial
temperature of the mixture is 73°F, the patching ma-
terial must be placed over the rupture within 12 min-
utes. Once the resin and the hardener are mixed, the
chemical reaction cannot be stopped. Therefore, the
patch should be completely applied before kick-over
occurs.
Figure 2-24 shows the relationship of the kick-
over time to the resin temperature. If you know the
resin temperature at the time of mixing, you are able
to determine the amount of time available to apply the
patch before kick-over occurs. You can see in figure
2-24 that if the resin temperature is 80°F (point A), the
kick-over will occur in less time than if the resin
temperature were 60°F (point B). The difference in
resin temperatures represents an application working
time of 9 minutes instead of 18 minutes.
NOTE
If the initial resin temperature exceeds
80°F, the temperature should be reduced by
artificial means to 73°F before mixing. This
lowering of the temperature allows for addi-
tional application working time.
Advantages of the Plastic Patch
From the damage control viewpoint, the main
advantages of the plastic patch are (1) versatility, (2)
simplicity, (3) effectiveness, (4) speed of application,
and (5) durability.
The plastic patch can be successfully applied to a
variety of damaged surfaces, whether with smooth
edges or jagged protruding edges. Since the plastic
has excellent adhesive qualities, it can be readily ap-
plied to steel, cast iron, copper, copper-nickel, brass,
bronze, and galvanized metals.
It is easy to prepare the plastic materials and to
apply the plastic patch. By following the instructions
outlined in the instruction manual that is included in
the kit, anyone with little or no experience can readily
prepare the materials and apply a plastic patch. A
plastic patch is applied in much the same way as a
battle dressing is used in first aid.
If the materials are properly prepared and the
application procedures are followed, the plastic patch
will be 100 percent effective. If leakage occurs
through a plastic patch, it is likely that propr prepa-
ration and application procedures have not been fol-
lowed.
The speed of application varies somewhat with
the size and type of rupture, and with local working
conditions. When proper preparation procedures are
followed, a simple patch can be applied to a 4-inch
pipe by an inexperienced crew who have had the
minimum amount of training and indoctrination in 10
minutes or less. The type and the size of the rupture or
the shape and the size of the structure to which the
patch is applied do not materially affect the time
involved in patching, but some types of damage may
require more initial preparation.
The maximum period of effectiveness of a plastic
patch is not known, but all indications are that a
properly applied patch can last indefinitely or cer-
tainly until permanent repairs can be made. The patch
is relatively inert, being seriously affected only by
excessive heat and concentrated acids.
2-16
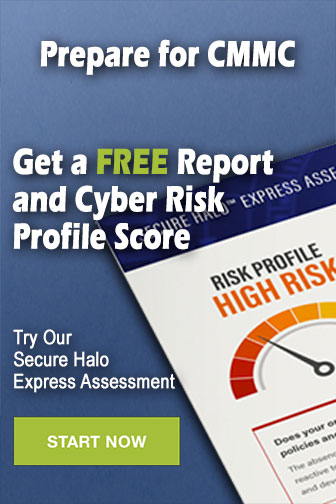