amount of resins and hardeners. For example, a 2-inch
rupture in a 2-inch diameter pipe requires 500 grams of
activated resin and a length of woven roving cloth at
least 25 inches long. Cut the woven roving cloth, in
width, to extend at least 3 to 4 inches on either side of
the rupture.
Simple Pipe Patch. The following numbered
instructions are step-by-step procedures for applying
the simple pipe patch;
1. Put on the eyeshields and the gloves, then open
the liquid resin can and the liquid hardener can.
2. Add hardener to the resin and mix thoroughly
for approximately 2 minutes or until a uniform gray
color is observed. (Note that the entire contents of the
liquid hardener in the smaller can is the correct propor-
tion for mixing with the entire contents of the larger can
of liquid resin.)
3. Coat both sides of the void cover with the resin
hardener mixture and tie the void cover over the rupture
with chalk line (view A of fig. 2-26).
4. Lay the woven roving cloth on a clean, flat
surface. Starting at one end of the cloth, pour on resin-
hardener mixture and spread evenly over the entire
surface of the cloth using the spatula provided in the kit.
It is only necessary to impregnate one side of the woven
roving cloth, but be careful to ensure the edges are well
impregnated with the resin-hardener mixture.
5. Center the woven roving cloth over the void
cover with the impregnated side toward the pipe and
wrap around the pipe not less than three turns and
preferably not more than four turns. See view B of
figure 2-26.
6. Wrap the PVC film around the entire patch,
making at least two complete turns. Tie the PVC film
with the chalk line, starting from the center of the patch
and working toward one end, making 1/2-inch spacings
between spirals (view C of fig. 2-26). Tie this end
securely but do not sever the line. Make one spiral back
to the center of the patch, then, working to the opposite
end from the center of the patch, make 1/2-inch spacings
between spirals and again secure the line. After 30 to 40
minutes, the patch should be sufficiently cured to re-
store the pipe to service.
7. Remember that for best results the temperature
of the liquid resin and the liquid hardener, before mix-
ing, should be approximately 70°F. With a temperature
of 70°F at the time of mixing, the patch cures in approxi-
mately 1 hour from the initial mixing time.
Figure 2-26.Simple pipe patch.
8. In emergencies, if the temperature of the resins
and the hardeners is below 50°F, kick-over may be
accelerated by applying external heat with hot air heat-
ers, infrared lamps, or light bulbs. The external heat
must be applied gradually because excessive applica-
tion of heat causes the plastic patch to be extremely
porous. Before mixing, it is better to warm the resin and
hardener in the can to a temperature of about 70°F.
9. Be careful not to restore pressure to the piping
system too soon. In general, pressure may be restored
when you can hold your hand on the entire patch area
without discomfort resulting from heat. Normally this
may require between 30 to 40 minutes after kick-over,
or 50 to 60 minutes from the initial mixing time.
2-18
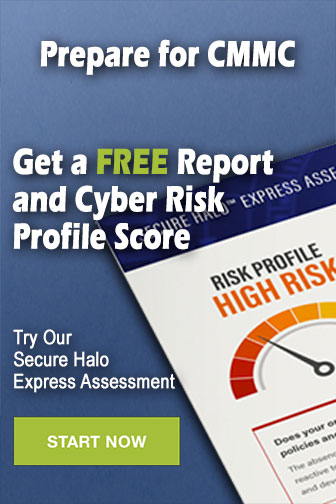