between the threaded bolt and end cap to prevent leak-
age at this point.
Both the base cap and the end cap have projecting
knife edges. When the elements are mounted on the
standpipes, the projecting knife edges are forced into
the synthetic rubber gaskets on each end of the ele-
ments, forming a tight seal.
COALESCING ELEMENT. The coalescing
element is a cylindrical unit 24 inches long and 3 5/8
inches in diameter. It consists basically of a pleated
paper element encased by fiberglass wrappings. The
fiberglass is held in place by a cloth sleeve. Each end
has a synthetic rubber gasket to form a tight seal and
ensure flow through the element when mounted. Flow
through a coalescer element is inside to outside.
SEPARATOR ELEMENT. The separator ele-
ment has practically the same dimensions as the coa-
lescer, but it is constructed of a different material. It
consists basically of a perforated inner brass core cover
with a 200-mesh, monel, Teflon-coated screen. This
screen is enclosed by an additional aluminum screen.
Separator elements are considered permanent and only
require cleaning, unless they are damaged, in which
case they must be replaced. Flow through a separator
element is outside to inside.
Installing Elements. To install an element on
the element mounting assembly, proceed as follows:
1. Make sure the gaskets are in place, then slide the
element over the perforated standpipe.
2. Attach the end cap, with metal and fiber gasket
in place, and install the threaded bolt fingertight.
3. Center the element on the mounting assembly,
and tighten the end cap bolt. The bolts should be torqued
to 12 foot-pound or 144 inch-pound.
4. Check the element for tightness.
FILTER INLET CHAMBER. Fuel enters the
filter initially at the inlet chamber. This chamber of the
filter is dome-shaped to provide a uniform flow of fuel
to all coalescing elements simultaneously. From the
inlet chamber the fuel passes through the tube sheet into
the coalescing elements in the fallout chamber.
FALLOUT CHAMBER. The fallout chamber is
the center section of the filter shell. It is the largest of
the three filter chambers. This area of the filter is pro-
vided to allow the coalesced water to fall out of the fuel
stream by gravity as it flows from the coalescer ele-
ments to the separator elements. Both sets of filter
elements are installed in this chamber.
The fallout chamber also contains a manhole cover,
filter vent line, and water receiving sump.
The coalescing stage is the first stage of filtration.
It consists of a number of individual coalescer elements
mounted in symmetrical arrangement on the inlet tube
sheet. The fuel leaving the inlet chamber must pass
through these elements from the inside to outside before
entering the fallout chamber. As the fuel passes through
the elements, they perform the dual function of remov-
ing solid contaminants from the fuel and coalescing
water.
A bolted manhole cover with gasket is installed on
the side of the filter shell. This opening is provided to
allow personnel to gain entrance to the fallout chamber
for replacing elements and maintenance.
A filter vent line is installed at the extreme top of
the fallout chamber. This line, fitted with a bulls-eye
sight glass, two shutoff valves (one on each side of the
sight glass), and a one-way check valve, directs fuel
back into the contaminated settling tanks or overboard.
The filter is vented until a solid stream of fuel is ob-
served in the sight glass.
The separator stage is the second stage of filtration.
It consists of a number of individual separator elements
mounted in symmetrical arrangement on the outlet tube
sheet.
Fuel leaving the fallout chamber must pass through
the separator elements from the outside to the inside
before entering the outlet chamber. As the fuel passes
through these elements, they repel the final traces of
water from the fuel stream. In addition to this primary
function, the separator elements also serve as a final
filter if one or more coalescer elements rupture. But,
separator elements can only filter solids larger than 10
microns.
Water Receiving Sump. The filter sump is lo-
cated at the bottom of the filter vessel. The sump re-
ceives the water that has been separated from the fuel.
A reflex type sight glass is installed on one side of
the sump for observing the water level within. Shutoff
valves are installed in the connecting piping for isolat-
ing the sight glass during maintenance.
Centrally located on the side or the bottom of the
sump is a flanged opening to which is bolted a rotary
control valve. This valve is attached to, and mechani-
cally operated by, a ball float housed within the filter
sump. The float-operated rotary control valve is a part
of the filter automatic hydraulic device. It will be
explained in detail later in this section.
OUTLET CHAMBER (CLEARWELL). This
section of the filter is commonly called the clear-well
because the fuel here is clear of contaminants. It has a
4-28
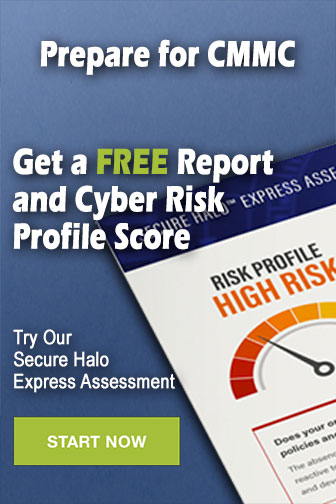