system. After off-loading of gasoline, the tanks are
flushed with seawater to rid the tanks of traces of
liquid gasoline. Three complete changes of seawater
are required to ensure proper flushing.
To flush the tanks, use the following procedures:
1. Strip the outer and draw-off tanks as described
in the earlier section for stripping procedures.
2. Make sure the following valves are closed:
a. Tank seawater supply line steam-out valve.
b. Sea chest steam-out valve.
3. Open the following valves:
a. Seawater elevated loop overboard discharge
valve.
b. Seawater equalizing tank valve.
c. MOGAS tank seawater supply valve.
d. Seawater sea chest valve.
4. Start the seawater compensating pump, then
open the discharge valve to fill the tanks with seawater.
5. When seawater is visible in the sight glass in the
fill line, close the tanktop valve.
6. Stop the seawater compensating pump when the
equalizing tank is full:
a. Close the discharge valve.
b. Close and lock the sea chest valve.
7. Complete the deballasting and filling evolution
three times.
8. Report that flushing is complete.
After the tanks are emptied of all seawater, they
are steamed to get rid of all traces of gasoline vapor.
The tanks are coated with a zinc base that is not
damaged by steam.
The procedures for steaming the tanks are as fol-
lows:
1. Close all valves in the system.
2. Connect a steam hose to the steam-out connec-
tion in the seawater supply line.
3. Open the following:
a.
b.
c.
d.
Tanktop fill valve.
Fill line isolation valve.
Flow meter bypass.
Filling station isolation valve.
NOTE
The system will be vented overboard from
the most remote fueling station.
4. Remove the hose from the reel at the fuel station.
5. Commence steaming:
a. Steam the tank for 6 to 12 hours.
b. The temperature must not exceed 240°F.
c. Low-pressure air is injected with the steam
to control the temperature and assist in forcing the steam
through the piping.
6. Test the steam exhaust. (This is done by the Gas
Free Engineer, using a Combustible Gas Indicator.)
7. When a negative reading is obtained, secure the
steam and allow the tank and piping to cool.
8. Remove a positive stop valve close to the steam-
out connection and check for damage.
The distribution piping must be steamed and gas
freed for major maintenance such as welding, brazing,
etc. Steam-out procedures for the distribution piping
are as follows:
1. Connect a steam hose to the gasoline pump
suction header steam-out connection.
2. Make sure the following valves are closed to
prevent steam from entering the drawoff tank:
a. Tanktop valve.
b. Tanktop recirculating valve.
c. Tanktop drain line.
3. Replace the pressure regulator and a transfer
pump with a spool. (This prevents damage to the seals
and rotating element of the pump).
4. Open the valves in the distribution riser from the
gasoline pump suction to the most remote fuel station:
a.
b.
c.
d.
e.
Transfer pump inlet and discharge.
Filter bypass.
Venturi discharge.
Flow meter bypass.
Station isolation valve.
6-25
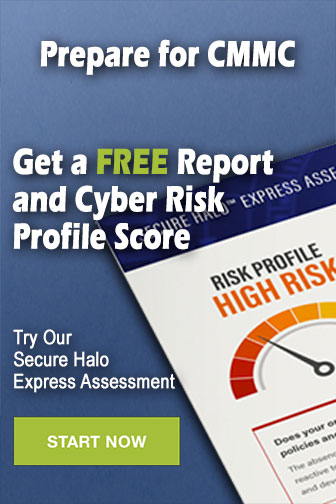