authorization to assign blocks of serial numbers for
different classes of material. Some examples of these
material classes are aviation repairable items, ordnance,
and food. Activities authorized to assign blocks of
numbers will have this segment subdivided to include
separate sections for each material class. The serial
numbers in each section run consecutively throughout
the fiscal year. As a minimum, the expenditure record
log will contain the following information:
Expenditure document number
Expending department
Material disposition
Material identification
Remarks
EXPENDITURE FILE
This file contains the original copies of transaction
documents processed by the activity. If the original is
not available, the activity may use a copy of the
transaction document. The transaction documents
referred to in this section are the forms used for each
transfer, cash sale, or survey. The sequence for filing the
invoices is Julian date and serial number sequence. The
retention period of the expenditure invoice file is 3 years
after completion of the expenditure transaction.
MATERIAL ISSUES
The term issue means the process of expending
material in response to a requisition from a user,
supported unit, or activity. Refer to issue processing
procedures described in NAVSUP Publication 1,
Volume 2 (shore), and NAVSUP Publication 485
(afloat). For mechanized activities, refer to the
publications and system procedures set.
Issues Ashore
Naval air stations and other stations under the
management of Naval Air Systems Command
(NAVAIR) use MILSTRIP for internal procedures. The
Naval Aviation Maintenance Program (NAMP)
procedures are also mandatory at naval air stations.
Document processing of material issues at supply
departments ashore generally follows the preposting
method. However, supply departments may establish
the postposting method for issuing material in direct
support of a weapons system. This method is necessary
to meet the time frame for processing requirements.
The chronological order of requisition processing
procedures ashore may vary among supply activities.
For example, mechanized processing involves different
organizational areas than does manual processing. The
processing of onstation issues by using the requestors
requisitions differs from the processing of offstation
requisitions. Receipts from offstation may be on DD
Form 1348-1, DD Form 1348-1A, or other shipment
documents.
The processing and routing of requisitions also
depend on the setup of the supply organization. Some
supply departments carry material in stock while others
get material support from the nearest stock point. Supply
departments that have material in stock route copies of
requisitions to either the issue control branch or the
stock control branch. The issue control branch reviews
the requisitions for proper MILSTRIP format and
determines the internal handling precedence. When
necessary, the issue control branch may provide
expediting services to quicken the processing. The issue
control branch also monitors the flow of issue
documents through the issue process and furnishes
status to requisitioners. This branch also maintains the
requisition history and status file and serves as liaison
between the supply department and its customers.
In screening the requisition, the issue control branch
checks for proper format, completeness of required data,
and proper authority. This branch also determines the
necessity for special handling. After the screening
process, the issue control branch forwards the
requisition to the stock control branch for further
processing. The issue control branch may return
requisitions that have errors to the originator for
resubmission. In some cases, the issue control branch
can correct the errors on the requisition. The action taken
in handling erroneous requisitions depends upon the
circumstances and local policy. For example, issue
control cannot ensure the correct data to use for the
missing information on a requisition. The issue control
branch should return the requisition to the originator for
correction. When possible, issue control may contact the
originator for the required data to correct the requisition.
Upon receipt of the requisition, the stock control
branch ensures that copies of request forms are intact.
The form used may be the DD Form 1348 (6 pt) or DD
Form 1149. (For automated activities, refer to the users
manual.) The stock control branch determines the
supply action to be taken on the requisition. If all
material is to be issued from stock, stock control sends
copies 2, 4, 5, and 6 of DD Form 1348 or 1149 to the
storage branch. Copies 7 and 8 of DD Form 1149 may
be used locally or destroyed.
If the entire requested quantity is issued from stock,
the storage branch can discard copy 2. After completing
the issue from stock the issue control branch retains and
files the proof of delivery copy.
7-2
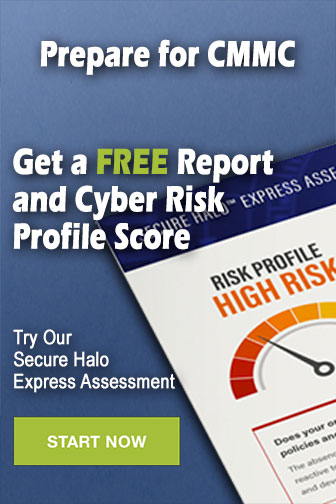