material to and from supported activities. Also, this unit
is responsible for planning and scheduling deliveries to
meet the required time frame. Fragile material and
delicate components that require special handling,
special padding, or racks should be delivered by the
most direct route to reduce the risk of damage.
The MDU processes requisitions as follows:
Upon receipt of requisitions for carried items from
SLU, MDU delivers the requisitions to the storage
location. The MDU picks up the material from the
storage location and delivers the items to the customer.
Upon issue of consumable material, storage personnel
detach the original and green copy of the DD Form 1348
(6 pt). Storage personnel put the Julian date and time of
issue below block V on the DD Form 1348 (6 pt). The
MDU sends copies of the DD Form 1348 (6 pt) to stock
control for financial and data processing actions. When
MDU delivers a repairable item, it requires an
immediate exchange or proof of previous turn-in unless
the item is listed in the CRIPL or the requisition contains
project code ZA9.
Upon delivery of the material, MDU will have the
customer sign and put the date and time on the pink and
hardback copy of the DD Form 1348(6 pt). The MDU
gives the pink copy to the customer and delivers the
hardback copy to RCU. If the material issued is a
repairable item, MDU will pickup the turn-in item and
all associated documents. Documents that may
accompany the item include the MAF (or facsimile),
service record card, or logbook. The MDU delivers the
part and documents to the aeronautical material
screening unit (AMSU) via the supply screening unit
(SSU). The MDU returns a signed and annotated copy
of the MAF (if used) and the original, green, and
hardback copies of the DD Form 1348 (6 pt) to DCU.
If the turn-in repairable is not available, MDU will
have the customer sign the yellow and hardback copies
of the DD Form 1348 (6 pt), which are then forwarded
to DCU. The MDU will give the pink copy of the DD
Form 1348 (6 pt) to the customer.
The MDU will receive the original, pink, yellow,
and hardback copies of the DD Form 1348 (6 pt) for
EXREP or work stoppage requisitions. The MDU will
pick up the repairable turn-in item with the associated
documents and give the signed yellow copy to the
customer as proof of turn-in. The MDU delivers the
turn-in item, associated documents, and the original,
pink, and hardback copies of the DD Form 1348(6 pt)
to SSU.
The MDU may sign the local form/log when picking
up repairable turn-in items before a requisition is
processed by RCU. The MDU delivers the item and
associated documents to AMSU, and gives the MAF
copy (if used) to DCU.
In activities that use the preposting method, MDU
may receive the requisitions from stock control or the
warehouse. In this case, the DD Form 1348 original and
green copies are deleted from MDU procedres.
The MDU also delivers material received from off
station. Upon receipt of the material in supply, receiving
personnel inform SRS. The SRS ensures that proper
documentation is attached for delivery of the material.
The SRS makes the appropriate entries on the
requirements register, file, or log concerning the receipt.
In activities that use the preposting method, MDU
delivers the DD Form 1348 (6 pt) marked warehouse
refusal to TRU via RCU for processing.
NOTE: The NALCOMIS activities use the DD
Form 1348-1 as an issue document. Distribution and use
of DD Form 1348-1 copies may vary at each activity.
PRE-EXPENDED BIN (PEB) UNIT. The PEB
unit contains high-usage, maintenance-related
consumable materials that have been expended from the
supply department stock records and financial accounts.
The purpose of the PEB is to shorten the issue and
accounting procedures for recurring issues of
maintenance-related materials. The PEBs are located
where they are readily accessible to maintenance
personnel and, when feasible, where they can be
observed by the retail outlet storekeeper to aid in
recognizing abuses to the pre-expended system.
Items subject to pilferage are retained within an
enclosure with access limited to authorized personnel.
The SRS is responsible for the management and
maintenance of the PEB. This includes the
replenishment or turn-in action, as required. The PEB
stock is limited to maintenance-related material having
a minimum demand frequency of three per month. The
quantity of each item pre-expended may not exceed an
estimated 30-day supply, subject to the requirement that
stock be replenished in-full package quantities.
The supply officer and the maintenance officer of
the supported activity are jointly responsible for
determining eligible items in the PEB. his includes
items to be added or purged from pre-expended stocks.
Eligible items with a unit cost of 0 or less may be
routinely established in PEB stock. Eligible items with
9-8
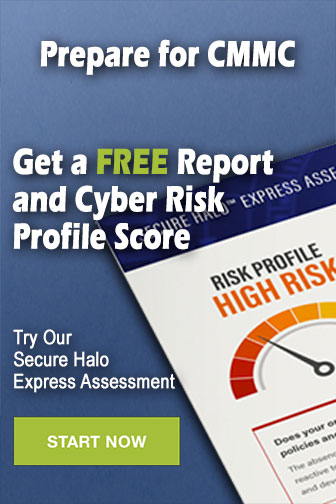