particles, and the steel is hardened. The fact that the
carbide particles can be dissolved in austenite is the
basis of the heat treatment of steel. The temperatures at
which this transformation takes place are called the
critical points, and vary with the composition of the
steel. The clement normally having the greatest
influence is carbon. The various heat-treating
procedures for commonly used aircraft steels are
outlined in Aerospace MetalsGeneral Data and Usage
Factors, NAVAIR 01-1A-9.
Forms of Heat Treatment of Steel
There are different forms of heating ferrous
materials such as steel. The methods covered in this
chapter are hardening, quenching, tempering, annealing
and normalizing, and case hardening. Terms such as
carburizing, cyaniding, and nitriding are also
discussed.
HARDENING.Heat treatment considerably
transforms the grain structure of steel, and it is while
passing through a critical temperature range that steel
acquires hardening power. When a piece of steel is
heated slowly and uniformly beyond a red heat, its
appearance will increase in brightness until a certain
temperature is reached. The color will change slightly,
becoming somewhat darker, which may be taken as an
indication that a transformation is taking place within
the metal (pearlite being converted into austenite).
When this change of state is complete, the steel will
continue to increase in brightness, and if cooled quickly
to prevent the change from reversing, hardness will be
produced. If, instead of being rapidly quenched, the steel
is allowed to cool slowly, the metal will again pass
through a change of state, and the cooling rate will be
momentarily arrested.
To obtain a condition of maximum hardness, it is
necessary to raise the temperature of the steel
sufficiently high to cause the change of state to fully
complete itself. This temperature is known as the upper
critical point. Steel that has been heated to its upper
critical point will harden completely if rapidly
quenched; however, in practice, it is necessary to exceed
this temperature by approximately 28° to 56°C (50° to
100°F) to ensure thorough heating of the inside of the
piece. If the upper critical temperature is exceeded too
much, an unsatisfactory coarse grain size will be
developed in the hardened steel.
Successful hardening of steel will largely depend
upon the following factors:
1. Control over the rate of heating, specifically to
prevent cracking of thick and irregular sections
2. Thorough and uniform heating through sections
to correct hardening temperatures
3. Control of furnace atmosphere, in the case of
certain steel parts, to prevent scaling and decarburiza-
tion
4. Correct heat capacity, viscosity, and temperature
of quenching media, to harden adequately and to avoid
cracks
When heating steel, you should use accurate instru-
ments to determine the temperature. At times, however,
such instruments arc not available, and in such cases,
the temperature of the steel may be judged approxi-
mately by its color. The temperatures corresponding to
various colors are given in table 15-1; however, the
accuracy with which temperatures may be judged by
colors depends on the experience of the worker and on
the light in which the work is being done.
QUENCHING PROCEDURE.A number of
liquids may be used for quenching steel. Both the media
and the form of the bath depend largely on the nature of
the work to be cooled. It is important that a sufficient
quantity of the media be provided to allow the metal to
be quenched without causing an appreciable change in
the temperature of the bath. This is particularly
important where many articles are to be quenched in
succession.
The tendency of steel to warp and crack during the
quenching process is difficult to overcome because
certain parts of the article cool more rapidly than others.
Whenever the transformation of temperature is not
uniform, internal strains arc set up in the metal that result
in warping or cracking, depending on the severity of the
strains. Irregularly shaped parts are particularly
susceptible to these conditions, although parts of an even
section are often affected in a similar manner.
Operations such as forging and machining may set up
internal strains in steel parts; therefore, it is advisable to
normalize articles before attempting the hardening
process. The following recommendations will greatly
reduce the warping tendency and should be carefully
observed:
1. An article should never be thrown into the bath,
By permitting it to lie on the bottom of the bath, it is apt
to cool faster on the top side than on the bottom side,
thus causing it to warp or crack.
2. The article should be slightly agitated in the bath
to destroy the coating of vapor, which might prevent it
from cooling rapidly.
15-40
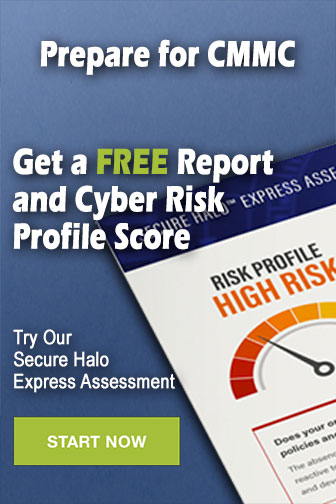