still air. Drafts will result in uneven cooling, which will
again set up strains in the metal.
Prolonged soaking of the metal at high temperatures
must be avoided, as this practice will cause the grain
structure to enlarge. The length of time required for the
soaking temperature will depend upon the mass of metal
being treated.
CASE HARDENING.In many instances, it is
desirable to produce a hard, wear-resistant surface or
case over a strong, tough core. Treatment of this kind
is known as case hardening. This treatment may be
accomplished in several ways; the principal ways being
carburizing, cyaniding, and nitriding.
Carburizing.When steel is heated, the pores of the
metal expand, allowing it to absorb any gases to which
it is exposed. By heating steel while it is in contact with
a carbonaceous substance, carbonic gases given off by
this material will penetrate the steel to an amount
proportional to the time and temperature.
The carburizing process may be applied to plain
carbon steels provided they are within the low-carbon
range. Specifically, the carburizing steels are those that
contain no more than 0.20 percent carbon. The lower the
carbon content in the steel, the more readily it will
absorb carbon during the carburizing process.
The amount of carbon absorbed and the thickness
of the case obtained increase with time; however, the
carburization progresses more slowly as the carbon
content increases during the process. The length of time
required to produce the desired degree of carburization
and depth of the case depend upon the composition of
the metal, the kind of carburization material used, and
the temperature to which the metal is subjected. It is
apparent that in carburizing, carbon travels slowly from
the outside toward the center; therefore, the proportion
of carbon absorbed must decrease from the outside to
the center.
A common method of carburizing is called pack
carburizing. When carburizing is to be done by this
method, the steel parts are packed with the carburizing
material in a sealed steel container to prevent the solid
carburizing compound from burning and retaining the
carbon monoxide and dioxide gases. The container
should be placed in a position to allow the heat to
circulate entirely around it. The furnace must be brought
to the carburizing temperature as quickly as possible,
and held at this heat from 1 to 16 hours, depending upon
the depth of the case desired and the size of the work.
After carburizing, the container should be removed and
allowed to cool in the air, or the parts removed from the
carburizing compound and quenched in oil or water. The
air coding, although slow, reduces warpage, and is
advisable in many cases.
In another method of carburizing, called gaseous
carburizing, a carbonaceous material is introduced into
the furnace atmosphere. When the steel parts are heated
in this carburizing atmosphere, carbon monoxide
combines with the iron to produce results that are
practically the same as those described under the pack
carburizing process.
Cyaniding.Steel parts maybe surface hardened by
heating while in contact with a cyanide salt, followed by
quenching. Only a thin case is obtained by this method;
therefore, it is seldom used in connection with aircraft
construction or repair. However, cyaniding is a rapid
and economical method of case hardening, and maybe
used in some instances for relatively unimportant parts.
The work to be hardened is immersed in a bath of molten
sodium or potassium cyanide from 30 to 60 minutes. The
cyanide bath should be maintained at a temperature of
760° to 899°C ( 1,400° to 1,650°F). Immediately after
removal from the bath, the parts are quenched in water.
The case obtained in this manner is due principally to
the formation of carbides on the surface of the steel. The
use of a closed pot is required for cyaniding, as cyanide
vapors are extremely poisonous.
Nitriding.This method of case hardening is
advantageous because a harder case is obtained than by
carburizing. Nitriding can only be applied to certain
special steel alloys, one of the essential constituents of
which is aluminum. The process involves the soaking of
the parts in the presence of anhydrous ammonia at a
temperature below the critical point of the steel. During
the soaking period, the aluminum and iron combine with
the nitrogen of the ammonia to produce iron nitrides in
the surface of the metal. Warpage of work during
nitriding can be reduced by stress-relief annealing, and
by exposure to nitrogen at temperatures no higher than
538°C (1,000F). Growth of the work is similarly
prevented, but cannot be entirely eliminated, and some
parts may require special allowance in some dimensions
to take care of growth.
The temperature required for nitriding is 510°C
(950°F), and the soaking period from 48 to 72 hours. An
airtight container must be used, and it should be
provided with a fan to produce good circulation and
even temperature throughout. No quenching is required,
and the parts may be allowed to cool in air.
15-43
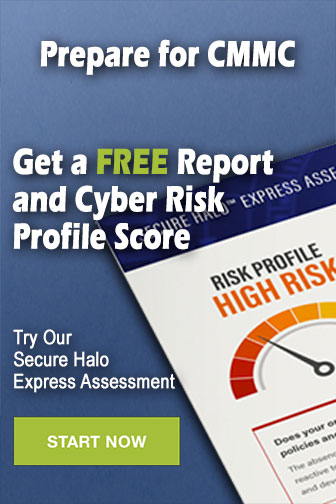