assigned Navy enlisted classification (NEC)
7225/military occupational specialty (MOS) 6044.
Organizational Maintenance Activities
O-levels responsibilities areas follows:
1. Request NDI I-level support as required.
2. Obtain IMA NDI services in all situations where
NDI results are suspicious.
3. Have an NDI technician verify defects
discovered by an NDI operator, whenever possible.
4. Inform the IMA, in advance, of scheduled NDI
requirements. Include these requirements in the monthly
maintenance plan.
5. O-level NDI technicians maybe assigned to the
supporting IMA, as necessary, to maintain their
proficiency and to augment IMAs NDI capabilities.
NDI INSPECTION METHODS
The various NDI methods serve as tools of
prevention that allow defects to be detected before they
develop into serious or hazardous failures. With the NDI
methods, a trained and experienced technician can
detect flaws or defects with a high degree of accuracy
and reliability. It is important that you become fully
knowledgeable of the capabilities of each method. It is
equally important that you recognize the limitations of
the methods. Some of the defects found by NDI include
corrosion, leaks, pitting, heat/stress cracks, and
discontinuity of metals. The following paragraphs will
give a brief synopsis of the various NDI inspections. For
further information on NDI procedures, you should
consult the Nondestructive Inspections Manual,
NA-01-1A-16, or the appropriate inspection manual
pertaining to the type of aircraft or part that is to be
inspected by an NDI method.
Magnetic Particle Inspection
Magnetic particle inspection is a rapid, non-
destructive means of detecting discontinuities in parts
made of magnetic materials. If the part is made from an
alloy that contains a high percentage of iron and can be
magnetized, it is in a class of metals called ferro-
magnetic, and it can be inspected by this method. If the
part is made of material that is nonmagnetic, it cannot
be inspected by this method. The magnetic particle
inspection method will detect surface discontinuities,
including those that are too fine to be seen with the naked
eye, those that lie slightly below the surface, and, when
special equipment is used, the more deeply seated
discontinuities.
The inspection process consists of inducing a
magnetic field into a part and applying magnetic
particles, in liquid suspension or dry powder, to the
surface being inspected. When the magnetic field is
interrupted by a discontinuity, some of the field is forced
out into the air above the discontinuity, forming a
leakage field. The leakage field will be stronger and
more concentrated the closer the discontinuity is to the
surface. The presence of a discontinuity is detected by
the ferromagnetic particles applied over the surface.
Some of these particles will be gathered and held by the
leakage field. This magnetically held collection of
particles forms an outline of the discontinuity and
indicates its location, size, and shape.
Electric current is used to create or induce magnetic
fields in magnetic materials. The magnetic lines of force
are always aligned at right angles (90°) to the direction
of the current flow. The direction of the magnetic field
can be altered, and it is controlled by the direction of the
magnetizing current. The arrangement of the current
paths is used to induce the magnetic lines of force so that
they intercept and are as near as possible at right angles
to the discontinuity.
The magnetic field must be in a favorable direction
to produce indications. When the flux lines are oriented
in a direction parallel to a discontinuity, the indication
will be weak or lacking. The best results are obtained
when the flux lines are in a direction at right angles to
the discontinuity. If a discontinuity is to produce a
leakage field and a readable magnetic particle
indication, the discontinuity must intercept the flux lines
of force at some angle. When an electrical magnetizing
current is used, the best indications are produced when
the path of the magnetizing current is flowing parallel
to the discontinuity, because the magnetic flux lines are
always at an angle of 90° to the flow of the magnetizing
current. The two types of magnetizing methods used are
circular and longitudinal.
CIRCULAR MAGNETIZATION.Circular
magnetization is used for the detection of radial
discontinuities around edges of holes or openings in
parts. It is also used for the detection of longitudinal
discontinuities, which lie in the same direction as the
current flow either in a part or in a part that a central
conductor passes through.
Circular magnetization derives its name from the
fact that a circular magnetic field always surrounds a
conductor, such as a wire or a bar carrying an electric
current (fig. 15-3). The direction of the magnetic lines
of force (magnetic field) is always at right angles to the
15-6
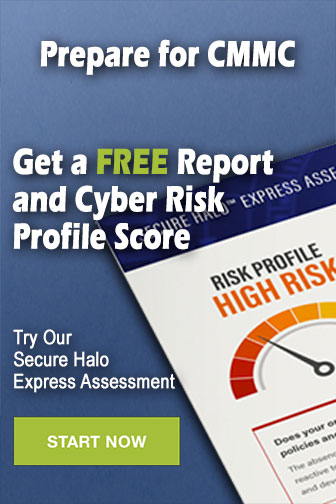