velocities encountered in jet power units. These alloys
are chemically similar to the previously mentioned
steels, but may also contain cobalt, copper, and
columbium in varied amounts as alloying elements.
NONFERROUS AIRCRAFT METALS
The term nonferrous refers to all metals that have
elements other than iron as their principal constituent.
This group includes aluminum, titanium, copper,
magnesium, and their alloys; and in addition, such alloy
metals as Monel and Babbitt.
Aluminum and Aluminum Alloys
Commercially pure aluminum is a white, lustrous
metal, light in weight and corrosion resistant. Aluminum
combined with various percentages of other metals
(generally copper, manganese, magnesium, and
chromium) form the alloys that are used in aircraft
construction. Aluminum alloys in which the principal
alloying ingredients are either manganese, magnesium,
or chromium, or magnesium and silicon, show little
attack in corrosive environments. On the other hand,
those alloys in which substantial percentages of copper
are used are more susceptible to corrosive action. The
total percentage of alloying elements is seldom more
than 6 or 7 percent in the wrought aluminum alloys.
TYPES, CHARACTERISTICS, AND USES.
Aluminum is one of the most widely used metals in
modern aircraft construction. It is vital to the aviation
industry because of its high strength/weight ratio, its
corrosion-resisting qualities, and its comparative ease of
fabrication. The outstanding characteristic of aluminum
is its light weight. In color, aluminum resembles silver,
although it possesses a characteristic bluish tinge of its
own. Commercially pure aluminum melts at the
comparatively low temperature of 1,216°F. It is
nonmagnetic, and is an excellent conductor of
electricity.
Commercially pure aluminum has a tensile strength
of about 13,000 psi, but by rolling or other cold-working
processes, its strength may be approximately doubled.
By alloying with other metals, together with the use of
heat-treating processes, the tensile strength may be
raised to as high as 96,000 psi, or to well within the
strength range of structural steel.
Aluminum alloy material, although strong, is easily
worked, for it is very malleable and ductile. It may be
rolled into sheets as thin as 0.0017 inch or drawn into
wire 0.004 inch in diameter. Most aluminum alloy sheet
stock used in aircraft construction ranges from 0.016 to
0.096 inch in thickness; however, some of the larger
aircraft use sheet stock that may be as thick as 0.0356
inch.
One disadvantage of aluminum alloy is the
difficulty of making reliable soldered joints. Oxidation
of the surface of the heated metal prevents soft solder
from adhering to the material; therefore, to produce
good joints of aluminum alloy, a riveting process is
used. Some aluminum alloys are also successfully
welded.
The various types of aluminum maybe divided into
two classes-casing alloys (those suitable for casting in
sand, permanent mold, and die castings) and the
wrought alloys (those that may be shaped by rolling,
drawing, or forging). Of the two, the wrought alloys are
the most widely used in aircraft construction, being used
for stringers, bulkheads, skin, rivets, and extruded
sections. Casting alloys are not extensively used in
aircraft.
WROUGHT ALLOYS.Wrought alloys are
divided into two classes-nonheat treatable and heat
treatable. In the nonheat-treatable class, strain
hardening (cold-working) is the only means of
increasing the tensile strength. Heat-treatable alloys
may be hardened by heat treatment, by cold-working, or
by the application of both processes.
Aluminum products are identified by a universally
used designation system. Under this arrangement,
wrought aluminum and wrought aluminum alloys are
designated by a four-digit index system.
The first digit of the designation indicates the major
alloying element or alloy group, as shown in table 1-2.
The lxxx indicates aluminum of 99.00 percent or
greater; 2xxx indicates an aluminum alloy in which
copper is the major alloying element; 3xxx indicates an
aluminum alloy with manganese as the major alloying
element; etc. Although most aluminum alloys contain
several alloying elements, only one group (6xxx)
designates more than one alloying element.
In the 1xxx group, the second digit in the
designation indicates modifications in impurity limits.
If the second digit is zero, it indicates that there is no
special control on individual impurities. The last two of
the four digits indicate the minimum aluminum
percentage. Thus, alloy 1030 indicates 99.30 percent
aluminum without special control on impurities. Alloys
1130, 1230, 1330, etc., indicate the same aluminum
purity with special control on one or more impurities.
Likewise, 1075, 1175, 1275, etc., indicate 99.75 percent
aluminum.
1-30
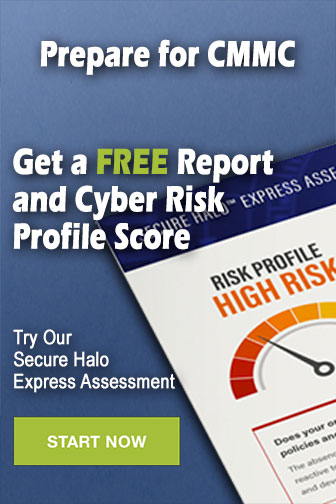