Table 1-1.SAE Numerical Index
Type of steel
Classification
Carbon
1xxx
Nickel
2xxx
Nickel-chromium
3xxx
Molybdenum
4xxx
Chromium
5xxx
Chromium-vanadium
6xxx
Tungsten
7xxx
Silicon-manganese
9xxx
Among the common materials used are ferrous metals.
HARDNESS TESTING METHODS.Hardness
The term ferrous applies to the group of metals having
iron as their principal constituent.
Identification
If carbon is added to iron, in percentages ranging up
to approximately 1.00 percent, the product will be vastly
superior to iron alone and is classified as carbon steel.
Carbon steel forms the base of those alloy steels
produced by combining carbon with other elements
known to improve the properties of steel. A base metal
(such as iron) to which small quantities of other metals
have been added is called an alloy. The addition of other
metals is to change or improve the chemical or physical
properties of the base metal.
SAE NUMERICAL INDEX.The steel
classification of the Society of Automotive Engineers
(SAE) is used in specifications for all high-grade steels
used in automotive and aircraft construction. A
numerical index system identifies the composition of
SAE steels.
Each SAE number consists of a group of digits, the
first of which represents the type of steel; the second,
the percentage of the principal alloying element; and
usually the last two or three digits, the percentage, in
hundredths of 1 percent, of carbon in the alloy. For
example, the SAE number 4150 indicates a
molybdenum steel containing 1 percent molybdenum
and 50 hundredths of 1 percent of carbon. Refer to the
SAE numerical index, shown in table 1-1, to see how
the various types of steel are classified into four-digit
classification numbers.
testing is a factor in the determination of the results of
heat treatment as well as the condition of the metal
before heat treatment. There are two commonly used
methods of hardness testing, the Brinell and the
Rockwell tests. These tests require the use of specific
machines and are covered later in this chapter. An
additional, and somewhat indirect, method known as
spark testing is used in identifying ferrous metals. This
type of identification gives an indication of the hardness
of the metal.
Spark testing is a common means of identifying
ferrous metals that have become mixed. In this test, the
piece of iron or steel is held against a revolving stone,
and the metal is identified by the sparks thrown off. Each
ferrous metal has its own peculiar spark characteristics.
The spark streams vary from a few tiny shafts to a
shower of sparks several feet in length. Few nonferrous
metals give off sparks when touched to a grinding stone.
Therefore, these metals cannot be successfully
identified by the spark test.
Wrought iron produces long shafts that are a duIl
red color as they leave the stone, and they end up a white
color. Cast iron sparks are red as they leave the stone,
but turn to a straw color. Low-carbon steels give off
long, straight shafts that have a few white sprigs. As the
carbon content of the steel increases, the number of
sprigs along each shaft increases, and the stream
becomes whiter in color. Nickel steel causes the spark
stream to contain small white blocks of light within the
main burst.
1-28
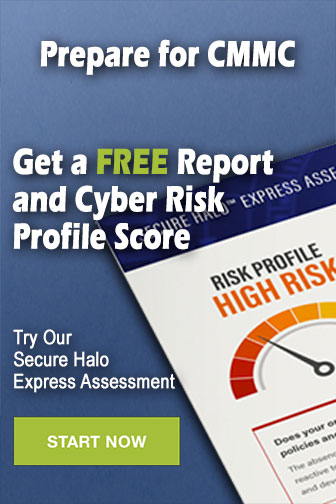