to reporting the work completed or signing off the
VIDS/MAF. If the tool cannot be located, notify the
maintenance officer or assistant maintenance officer via
the work center supervisor and maintenance control to
ensure that the aircraft or equipment is not released.
If the tool cannot be located after the maintenance
officers directed search, the person doing the
investigation will personally sign a statement in the
Corrective Action block of the VIDS/MAF that a lost
tool investigation was conducted and that the tool could
not be found. Subsequently, the normal VIDS/MAF
completion process will be followed.
The flight engineer/crew chief (senior maintenance
man in the absence of an assigned crew chief) will
assume the responsibilities of the work center
supervisor applicable to the TCP in the event of in-flight
maintenance or maintenance performed on the aircraft
at other than home station.
OCCUPATIONAL AWARENESS
Learning Objective: Identify sources of
information regarding hazards within the AM
rating and recognize terms applicable to
hazardous situations and materials.
Many different materials are used in the workplace.
Some are hazardous. You must know where to retrieve
information on these materials used in and around naval
aircraft. The MIMs give information on correct
maintenance practices, but may not always give
complete information regarding necessary safety
practices.
The Navy Occupational Safety and Health
(NAVOSH) program was established to inform workers
about hazards and the measures necessary to control
them. The Department of Defense has established the
Hazardous Material Information System (HMIS),
which is designed to acquire, store, and disseminate data
on hazardous material procured for use. The primary
source for you to get the necessary information before
beginning any operation involving the use of hazardous
material is the Material Safety Data Sheet (MSDS). The
MSDS, known as Form OSHA-20, is shown in figure
3-2. This nine-section form informs you of hazards
involved, symptoms of exposure, protective measures
required, and procedures to be followed in case of spills,
fire, overexposure, or other emergency situations.
The maintenance of safe and healthful working con-
ditions is a chain-of-command responsibility. Imple-
mentation begins with the individual sailor and extends
to the commanding officer. The chain-of-command
responsibilities are covered in OPNAVINST 5100.19B
and OPNAVINST 5100.23B.
Work center supervisors are responsible for training
work center personnel in the use of the MSDS.
Furthermore, they must ensure that personnel under
their supervision have been trained on the hazards
associated with the material and are equipped with the
proper protective equipment prior to using any
hazardous materials.
All sections of the MSDS form are important, and
contain information to accomplish a task without
causing damage to equipment or personnel. Always
ensure that you are using the correct MSDS with the
material being used. You should check the MILSPEC,
part number, federal stock number, and the name of the
manufacturer. Never use the MSDS with different
manufacturers. The formula for a given product may
differ and still meet the specifications requirements. The
handling and safety requirements will effectively
change based on different manufacturers.
Threshold Limit Value (TLV) in sections II and V
of the MSDS are established by the American
Conference of Governmental Industrial Hygienists
(CGIH). TLVS refer to airborne concentrations of a
substance and represent conditions that nearly all
workers may be exposed, day after day, without adverse
effects. You should know the effects of overexposure
and the emergency procedures required prior to using
any material.
We have been taught about incompatibility, such as
the mixing of oil and oxygen. Section VI (Reactivity
Data) of the MSDS contains a list of materials and
conditions to avoid that could cause special hazards.
Prompt cleanup of spills and leaks will lessen the chance
of personnel and the environment being harmed. Section
VII (Spill or Leak Procedures) of the MSDS lists the
required steps to be taken for cleanup and proper
disposal methods.
You should familiarize yourself and comply with
section VIII (Special Protective Information) of the
MSDS. In doing so, you will protect yourself and others
from dangerous exposure. Some protective equipments
are complex and require special training in proper use
and care. Never use a respirator that you have not been
tit-tested to wear. Always check to see that the cartridge
installed meets the requirements of the MSDS. If you
use a respirator you have not been trained for or fitted
to, or with the wrong cartridge installed, it can be as
dangerous to your health as wearing no protection at all.
3-3
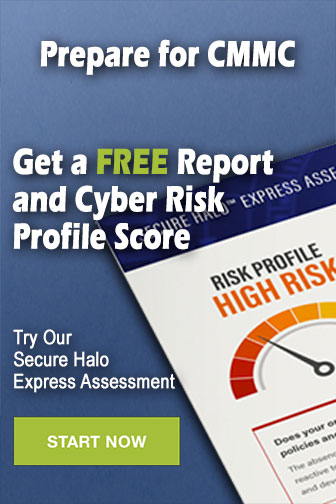