CAUTION
Do not heat the tank in excess of 110°F to seal
the injection groove as higher temperatures
are considered as a fire hazard.
The proper temperatures for sealing are 79° to 84°F.
If the tank is exposed to temperatures below 50°F, the
tank must be heated above 70°F before sealing is
attempted. This may be accomplished in a heated hangar
or by using portable heating units or electric blankets.
NOTE: If the sealing compound does not
appear after approximately 4 to 5 minutes, you
may assume that the compound is too cold, the
groove is plugged, or the surface gap is
excessive. In this case, the injection should be
discontinued until the discrepancy is remedied.
Testing
When an integral fuel cell has been repaired, it must
be pressure checked before it is filled with fuel. Since
the pressure testing procedure will vary with different
types of aircraft, you should always consult the
structural repair manual for the aircraft concerned for
the proper procedure. The following equipment is used
for pressure testing as system:
A source of nitrogen and a means of regulating
the nitrogen pressure
NOTE: The use of nitrogen for pressure testing
the fuel system is recommended since nitrogen
is an inert gas, and therefore presents no
explosive hazard when it is introduced into a
fuel cell containing fuel vapors. A source of dry
air is not recommended because it would
increase the ratio of oxygen to fuel vapor in the
cell, and the possibility of an explosion would
be increased.
Suitable hoses and fittings to connect the testing
equipment to fuel the system
A0 to 5 psi pressure gauge installed downstream
of the nitrogen supply
Miscellaneous plugs and caps for blocking
various lines and fittings
RECOMMENDED READING LIST
NOTE: Although the following references were
current when this TRAMAN was published, their
continued currency cannot be assured. Therefore, you
need to be sure that you are studying the latest revision.
Blueprint Reading and Sketching, NAVEDTRA
10077-F1, Naval Education and Training Program
Management Support Activity, Pensacola, Florida,
July 1988.
Fluid Power, NAVEDTRA 12964, Naval Education and
Training Program Management Support Activity,
Pensacola, Florida, July 1990.
Naval Aviation Maintenance Program, OPNAVINST
4790.2 (series), Office of the Chief of Naval
Operations, Washington, D.C.
Aviation Hydraulics Manual, NAVAIR 01-1A-17,
Commander, Naval Air Systems Command,
Washington, D. C., 1 February 1992.
General Manual for Structural Repair, NAVAIR
01-1A-1, Commander, Naval Air Systems
Command, Washington, D. C., 15 July 1969,
Change 11, 15 August 1989.
Technical Manual Structural Hardware, NAVAIR
01-1A-8, Commander, Naval Air Systems
Command, Washington, D. C., 1 September 1980,
Change 24, 15 October 1987.
Naval Occupation Safety and Health (NAVOSH)
Program Manual For Forces Afloat OPNAVINST
5100.19A, Commander, Naval Air Systems
Command, Washington, D. C., January 1983.
Naval Occupational Safety and Health (NAVOSH)
Program Manual, OPNAVINST 5100.23B,
Commander, Naval Air Systems Command,
Washington, D. C., August 1988.
Navy Support Equipment Common Basic Handling and
Safety Manual NAVAIR 00-80T-96, Commander,
Naval Air Systems Command, Washington, D. C., 1
April 81, Change 1, March 1986.
Technical Manual Index and Application Tables for
Aircraft Jacks, NAVAIR 19-70-46, Commander,
Naval Air Systems Command, Washington, D. C., 1
November 1989.
Technical Manual USN Aircraft Weight and Balance
Control, NAVAIR 01-1B-50, Commander, Naval
Air Systems Command, Washington, D. C., 1
October 1990.
3-50
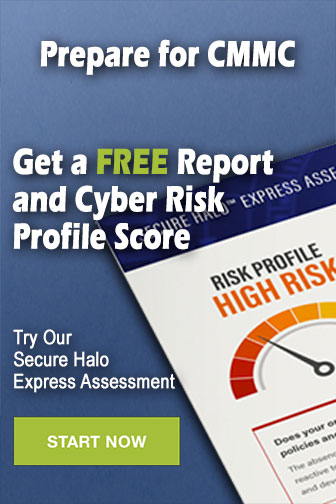