CHAPTER 4
HYDRAULIC CONTAMINATION AND RELATED
SERVICING/TEST EQUIPMENT
Chapter Objective: Upon completion of this chapter, you should have a working
knowledge of hydraulic contamination. You should be able to identify the support
equipment used in servicing, troubleshooting, repairing, and maintaining aircraft
hydraulic systems.
All modern naval aircraft contain hydraulic
systems that operate various mechanisms. The
number of hydraulically operated units depends upon
the model of aircraft. The average operational
aircraft has about a dozen hydraulically operated
units. Aircraft hydraulic systems are designed to
produce and maintain a given pressure over the entire
range of required fluid flow rates. The pressure used
in most Navy high-performance aircraft is 3,000 psi.
The primary use of hydraulic fluids in aircraft
hydraulic systems is to transmit power, but hydraulic
systems perform other functions. Hydraulic fluid acts
as a lubricant to reduce friction and wear. Hydraulic
fluid serves as a coolant to maintain operating temp-
eratures within limits of critical sealant materials, and
it serves as a corrosion and rust inhibitor. Critical
functions of hydraulic systems maybe impaired if the
hydraulic system fluid is allowed to become
contaminated beyond acceptable limits.
Hydraulic fluid contamination is defined as any
foreign material or substance whose presence in the
fluid is capable of adversely affecting the system
performance or reliability. Contamination is always
present to some degree, even in new, unused fluid.
Contamination must be below the level that adversely
affects system operation. Hydraulic contamination
control consists of requirements, techniques, and
practices that minimize and control fluid contami-
nation.
Remember the proverb, "An ounce of
prevention is worth a pound of cure."
HYDRAULIC CONTAMINATION
CONTROL PROGRAM
Learning Objective:
Recognize the Navy's
hydraulic contamination control program.
Hydraulic contamination in Navy and Marine
Corps aircraft and related support equipment (SE) is a
major cause of hydraulic system and component
failure.
Every technician who performs hydraulic
maintenance should be aware of the causes and
effects of hydraulic contamination. You should follow
correct practices and procedures to prevent
contamination.
Supervisory and quality assurance
personnel must know and ensure compliance with
accepted standards. Each maintenance level needs to
accept their applicable responsibility. Supervisory
personnel at each level of maintenance should
indoctrinate and train personnel and implement
procedures that apply to that level of maintenance.
The Hydraulic Contamination Control Program is
defined in the Naval Aviation Maintenance Program
(NAMP), OPNAVINST 4790.2 (series). Within the
scope of this program, training must be consistent
with the objectives of an effective aircraft hydraulic
system contamination control program. At all mainte-
nance levels, personnel must be trained in matters
pertaining to hydraulic systems contamination control
using Hydraulic Contamination Control Training
Device 4B38A or Videotape Number 802577DN.
The Hydraulic Contamination Control Program
requires you to follow the correct procedures during
fluid sampling, maintenance procedures, and
practices.
FLUID SAMPLING
Contamination measurement standards and
acceptability limits define and control hydraulic
contamination levels. The maximum acceptable
hydraulic fluid particulate level is Navy Standard
Class 5 for naval aircraft, and Navy Standard Class 3
for related SE. The contamination level of a
particular system is determined by analysis of a fluid
sample drawn from the system.
Analysis is
4-1
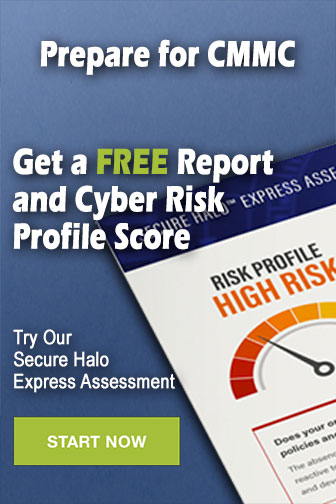