If packages of tubing, hoses, fittings, or
components are opened when received or found
opened, decontaminate their contents. Decontami-
nate the system if you suspect it is contaminated
(including water).
Keep the working area where
hydraulic components are repaired, serviced, or
stored clean and free from moisture, metal chips, and
other contaminants.
Perform required periodic
checks on equipment you use to service hydraulic
systems. Use hydraulic fluid MIL-H-46170 in
stationary hydraulic test stands.
TYPES OF CONTAMINATION
Learning Objective:
Identifiy the types of
hydraulic contamination found in naval
aircraft.
There are many different forms of contamination,
including liquids, gasses, and solid matter of various
composition, size, and shape. Normally, contami-
nation in an operating hydraulic system originates at
several different sources. The rate of its introduction
depends upon many factors directly related to wear
and chemical reaction. Contamination removal can
reverse this trend. Production of contaminants in the
hydraulic system increases with the number of system
components. The rate of contamination from external
sources is not readily predictable. A hydraulic system
can be seriously contaminated by poor maintenance
practices that lead to introducing large amounts of
external contaminants. Poorly maintained SE is
another source of contamination.
Contaminants in hydraulic fluids are classified as
particulate and fluid contamination. They may be
further classified according to their type, such as
organic, metallic solids, nonmetallic solids, foreign
fluids, air, and water.
PARTICULATE CONTAMINATION
The type of contamination most often found in
aircraft hydraulic systems consists of solid matter.
This type of contamination is known as particulate
contamination.
The size of particulate matter in hydraulic fluid is
measured in microns (millionths of a meter). The
largest dimensions (points on the outside of the
particle) of the particle are measured when
determining its size.
The relative size of particles,
measured in microns, is shown in figure 4-2.
Table 4-1 shows the various classes of particulate
contamination levels.
Contamination of hydraulic fluid with particulate
matter is a principal cause of wear in hydraulic pumps,
actuators, valves, and servo valves.
Spool-type
electrohydraulic valves have been used in particle
contamination experiments. The valves are easy to
control and respond rapidly to repositioning. In these
experiments, the valves were operated with both
ultraclean and contaminated hydraulic fluids. The
experiments proved that wear is accelerated by even
small amounts of contamination.
Contamination
increases the rate of erosion of the sharp spool edges
and general deterioration of the spool surfaces.
Because of the extremely close fit of spools in servo
valve housings, the valves are particularly susceptible
to damage or erratic operation when operated with
contaminated hydraulic fluid.
Figure 4-2. Graphic comparison of particle sizes.
4-4
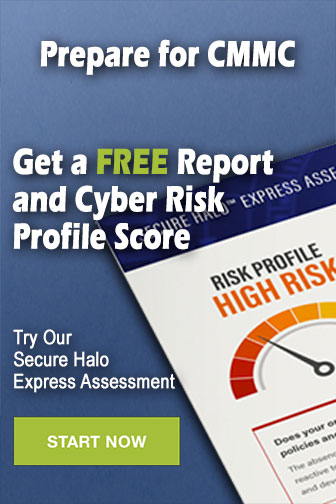