stationary swashplate.
When the primary servo
cylinders are actuated by the flight controls, the
stationary swashplate moves, with this movement
being transmitted to the rotating swashplate. The
rotating swashplate sends movement, through the
adjustable pitch control rods, to the sleeve spindle of
the rotary blades. This action changes the angle of
incidence of the blades.
ROTARY-WING MAINTENANCE
Learning Objective: Recognize general
rotary-wing maintenance procedures to
include system rigging and rotor blade
tracking.
Organizational maintenance of the helicopter
flight control system includes periodic inspection,
lubrication, rigging, and blade tracking. It also
includes the cleaning of the rotary-wing and rudder
blades and the removal and replacement of
malfunctioning components.
Organizational maintenance of the auxiliary and
primary servo cylinders is limited to minor adjust-
ment and replacement of miscellaneous seals.
Organizational maintenance includes the removal and
installation of the complete component. Major
adjustments made on servo cylinders during overhaul
are critical. These adjustments are not made at the
lower levels of maintenance.
Vibrations and cyclic actions inherent to
helicopters can cause component or structural fatigue.
Nondestructive testing (NDI) is used on many parts of
the airframe and many dynamic components to detect
flaws (cracks) that could lead to failure. Additionally,
most of the dynamic components, such as rotor heads,
blades, servo cylinders, and swashplates, have forced
(high-time) removal intervals. These time intervals
are listed by component in the Periodic Maintenance
Information Cards (PMIC) for the aircraft.
You should clean the rotary wing and rotary
rudder as necessary, using only approved cleaners.
The concentration of mixture will vary, depending on
the surface condition and type of cleaner used.
CAUTION
Both the rotary-wing and rudder blades
have areas that connect by bonding
adhesives or are manufactured out of fiber
glass or advanced composite materials.
Never use solvents or cleaners not
specifically authorized in the MIM. Do not
use lacquer thinner, naphtha, carbon
tetrachloride, or other organic compounds
for cleaning in these bonded areas. Use of
these solvents or cleaners may result in
blade failure.
SYSTEM RIGGING
Rigging checks and adjustments involve the
cyclic pitch control stick, collective pitch control
stick, and pedal positions. These controls must
coordinate with the correct rotary-wing and
rotary-rudder blade angles. You must be sure that the
flight controls are operating under normal friction
loads.
The use of rigging pins and other rigging aids
provide proper rigging and proper system operation.
Each step outlined in the MIM should be carefully
performed.
Several quick rigging, cable adjustment, and
operational checks with related maintenance
precautions are found in the MIM. No attempt to
duplicate this information is provided in this chapter.
The MIM should be consulted before any mainte-
nance begins.
At the completion of rigging, a flight test must be
performed by a qualified pilot. A flight check chart is
provided by the MIM. The MIM lists the conditions
of the check, the required performance, and informa-
tion to aid in the correction of malfunctions.
ROTOR BLADE TRACKING
You must perform blade tracking when rerigging
the helicopter. Tracking is necessary when the blades,
the main gearbox, or the main rotor head assembly
have been replaced. Unless the blades arc in proper
track, vibrations will occur in the helicopter with
every revolution of the main rotor. At high rpm
settings, these vibrations could cause serious struc-
tural damage.
10-11
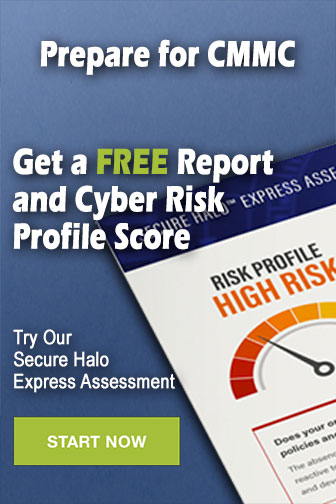