the vent and builds up brake pressure. When the
pressure increases beyond 200 psi, the shuttle valve in
the panel package shifts. Pressure is sent to the rotor
brake and blocks pressure from the automatic blade
folding system.
The panel package accumulator
reduces minor pressure surges during manual and
automatic operation. The accumulator maintains a
steady pressure to the brake. The relief valve relieves
pressure surges in excess of 600 psi.
Rotor Brake Accumulator
The spring-loaded rotor brake accumulator
permits manual operation of the master cylinder
handle during automatic blade folding operations.
Applying the automatic brake unseats the
accumulator sequence valve. The open valve permits
actuation of the master cylinder handle. The
hydraulic fluid flows through the sequence valve and
compresses the accumulator spring. Releasing the
automatic brake causes pressure to flow from the
accumulator to the panel package shuttle valve, and
repositions it. Simultaneously, the panel package
accumulator maintains hydraulic pressure that was
trapped from the automatic application in the rotor
brake. The rotor brake accumulator additionally
compensates for thermal expansion and contraction of
the fluid, and aids in dampening pressure surges.
Rotor Brake Master Cylinder
The master cylinder is gravity fed by hydraulic
fluid from the utility fluid tank. Move the brake
handle down and forward to apply pressure to the
system.
A spring latch on the cylinder linkage
automatically locks the handle in the ON or PARK
position. To release the brake, pull the latch and place
the handle in the DETENT position. The pressure
gauge indicates the amount of pressure produced by
the master brake cylinder. The check valve provides a
means to pressure bleed the system.
A minimum
pressure of 320 psi is required to effectively operate
the rotor brake.
AUTOMATIC BLADE FOLDING SYSTEM
An automatic blade folding system of a
representative helicopter is shown in figure 10-12.
This system is capable of automatic blade folding of
one of the two rotary blades from cockpit controls.
Blade Folding Operations
The No. 1 blade does not fold, but it automatically
positions over the tail pylon. The only hydraulic
actuation of the No. 1 blade is damper positioning.
The hydraulic portion of the system positions the
blades and folds the No. 2 blade. The electrical
portion of the system provides the sequencing of
operation of the various hydraulic components. It
acts to prevent accidental operation of the system.
Warning and indicating lights show the status of the
system at all times. Safe operation is maintained by a
series of electrical interlocks.
You should perform blade folding operations with
the pylon locked in the flight position and the engine
operating at 104 percent. The rotary-wing head must
not be operating.
The accessory drive switch is
placed in ACCESS DRIVE. The safety valve switch
is placed OPEN, and the master switch is placed ON.
The blade switch is placed in the FOLD position.
Hydraulic pressure from the utility hydraulic
system is 3,000 psi. The pressure flows through the
motor-operated safety valve. This pressure flows to
the blade positioner control valve, and is sent to the
blade positioner drive unit for engagement with the
rotor brake disc. This action turns the rotary-wing
shaft.
Pressure is sent through the blade rotation control
valve to the blade positioner hydraulic motor. The
motor revolves the blade positioner, causing the
rotation of the rotary-wing head. When the No. 1
blade is properly positioned aft, the blade positioner
control valve is energized in the opposite direction.
The action stops positioning and disengaging of the
blade positioner drive unit. Fluid is also sent to
engage the rotor brake at this time.
On later models, the rotor brake applies manually.
The blade fold control valve is energized, sending
hydraulic pressure through the rotor coupling to each
damper-positioner.
The blades move against their
autorotative stops.
The mechanical action of
positioning the blades operates the damper-positioner
sequence valves. These valves cause hydraulic fluid
to operate the control lock cylinder, locking the
controls.
With the rotor head controls locked,
pressure is sent to the blade fold lock cylinder. The
lockpin is retracted, and fluid is sent to the blade fold
cylinder.
10-15
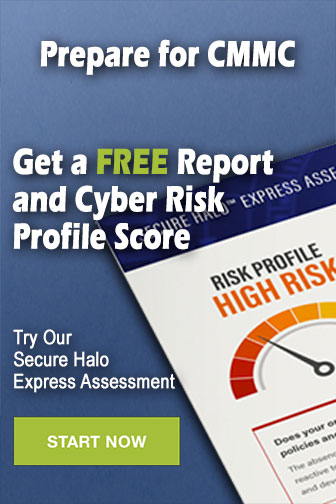