The blade fold cylinder is found inside the sleeve
spindle of the No. 2 blade. See figure 10-13. It
connects to sector gears, which cause the folding
actions.
When the No. 2 blade reaches a certain
angle, a microswitch turns on the blade folded light in
the cockpit. The lock valve traps hydraulic fluid in
the rotary-wing head to keep the damper-positioners
in the autorotative position. It also keeps the No. 2
blade in the folded position.
With the fold sequence completed, the SAFETY
VALVE OPEN, the FOLD PWR ON, the No. 1
BLADE POS, the CONT LOCKPIN ADV, and the
BLADES FOLDED warning and indicating lights are
lit.
NOTE: You may have to move the cyclic
control stick around the neutral position to
engage the control lockpin.
If excessive
movement of the cyclic stick is necessary,
troubleshoot the system for possible mal-
adjustment.
Blade Spreading Operations
The spreading operation requires the same
conditions as the fold operation.
The primary
exception is that the blade fold switch is in the
SPREAD position.
Pressure is sent through the
motor-operated safety valve and through the
positioning unit pressure reducers. Pressure is sent to
the blade positioner drive unit for rotor brake disc
disengagement and the engagement of the rotor brake.
With the rotor brake on and the blade fold valve
energized, 3,000 psi hydraulic fluid is sent through
the rotor coupling.
From the coupling, pressure is
sent to the damper-positioners. The damper-positioners
drive the blades against their autorotative stops.
Pressure is then sent to the blade fold cylinder. The
blade fold cylinder operates the gear sector and
spreads the blade. As the blade starts to spread, the
lock valve solenoid is de-energized, releasing fluid in
the rotary-wing head.
When the blade is completely spread, hydraulic
fluid is sent to the blade lock cylinder, engaging the
blade lockpin. Engagement and locking of the blade
lockpin causes the internal sequencing mechanisms to
direct pressure to the control lock cylinder. The
control lock cylinder, in turn, locks the controls. The
spread sequence is completed. The FOLD PWR,
BLADE SPREAD, and SAFETY VALVE OPEN
warning and indicating lights should be lit.
Figure 10-13.Blade fold cylinder.
Blade Folding System Components
Hydraulic components of the blade folding
system are conventional type, solenoid-operated
selector valves, check valves, pressure reducers and
snubber, sequence valves, and actuating cylinders. Of
special interest are the safety valve, the blade
positioner drive unit, the rotor coupling, the control
lock cylinder, and the blade fold accumulator.
SAFETY VALVE.The safety valve is a
two-position, motor-operated selector valve. The
purpose of the unit is to prevent hydraulic pressure
from entering the blade fold system during flight.
The motor provides a camming action to move the
poppet valve within the selector valve. With the rotor
stopped, electrical interlocks allow the safety valve to
send fluid to the blade folding system. This action
occurs when the safety valve switch is placed in the
OPEN position. In the CLOSED position, pressure is
blocked at the pressure port. The system vents
through the lock valve. The venting eliminates the
possibility of damage to the system by thermal
expansion of the hydraulic fluid. The safety valve
will not close if the blade spread interlock relay
malfunctions. The safety valve will not close if the
blades are folded. The safety valve motor opens a
limit switch. The switch cuts electrical power to the
motor when the safety valve reaches the fully open
position.
BLADE POSITIONER DRIVE UNIT.The
drive unit is found on the upper surface of the main
gearbox input cover.
It consists of a gear train, a
sequence valve, a tiller plug, a sight gauge, and a
hydraulic motor. The gear train rotates because of the
hydraulic motor. The gear train turns the rotary-wing
10-18
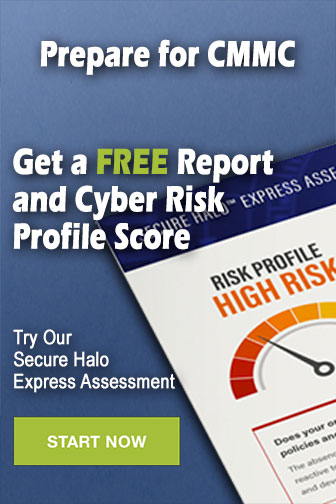