Tracking the blades is necessary to be sure that
the blades rotate in the same horizontal plane (track).
This is accomplished by pretrack rigging of the
rotary-wing head and by the use of pretracked blades.
Pretrack rigging involves adjusting the pitch
control rods until an exact sleeve angle (within
1 minute) is found on all sleeve spindles. A
micrometer type of decal is affixed to the adjustable
pitch control rods as a permanent reference at the
overhaul activity. A pretrack number is stenciled on
each blade at the time of manufacture or overhaul.
This number is based on the effective angle of the
blade. Install prctracked blades on the helicopter by
setting the adjustable pitch control rod to the pretrack
number stenciled on the blade.
If the pretrack number is MINUS and the pitch
control rod decal shows the setting is zero, loosen the
locknut.
Shorten the rod by rotating the tang
clockwise.
Keep rotating until it aligns (closest
notch) with the appropriate blade pretrack number on
the lower scale of the lower decal. Engage the tang by
tightening the locknut. If the pretrack number of the
blade is PLUS and the pitch control rod decal shows
the setting is zero, loosen the locknut. Lengthen the
rod by rotating the tang counterclockwise. Keep
rotating the tang until it aligns (closest notch) with the
appropriate blade pretrack number on the upper scale
of the lower decal. After adjusting the remainder of
the pitch control rods, tighten the locknuts to the
torque specified in the MIMs. Safety wire the
locknuts to the tang.
You should perform a ground operational check.
With the rotary-wing head engaged, operate the
engines at 100 percent. Check for vibrations in the
rotary-wing head.
If vibrations occur and the
adjustable pitch control rods were properly adjusted,
use an alternate method of blade tracking. In this
case, use a strobe blade tracker to check the blades
under actual operating conditions. You must be sure
that all blades are rotating in the same horizontal
plane. See figure 10-10. Pitch adjustment of each
blade may be made to compensate for blade
differences.
The Strobex blade tracker permits tracking from
inside the helicopter in flight or on the ground. The
system uses a highly concentrated stroboscopic light
beam flashing in sequence with rotation of the
rotary-wing blades, so that a fixed target at the blade
tips will appear to be stopped. A soft iron sweep
attached to the rotating swashplate passes close to a
magnetic pickup attached to the stationary
swashplate, causing a once-per-revolution pulse,
which synchronizes the lamp flash rate with the
rotation of the blades.
Each blade has a
retroreflective target number attached to the
underside of the blade in a uniform location.
Tracking of each blade is then determined by the
relative vertical position of the fixed target numbers.
See figure 10-10.
Consult the applicable aircraft
MIMs for the proper operating procedures for the
Strobex blade tracker. For maintenance infor-
mation on the Strobex tracker, refer to NAVAIR
17-15BBA-4.
NOTE: Do not adjust blades by the Strobex
method of blade tracking unless problems
result from normal tracking procedures.
ROTOR BRAKE SYSTEM
As a part of the blade folding operation, the rotor
brake applies manually or automatically. The system
is shown in figure 10-11. It consists of a rotor brake
assembly, panel package, accumulator, master
cylinder, pressure gauge, check valves, and pressure
switches.
Rotor Brake Assembly
The rotor brake assembly is comparable to the
single disc wheel brake in its design and operation.
Hydraulic actuation of the brake may be made
manually by using the rotor brake master cylinder
located in the cockpit. The brake applies
automatically during the blade folding operation by
the blade positioner control valve. In manual
operation, the brake is capable of stopping the
rotary-wing head in 14 seconds from 157 rpm.
Replace the brake linings when any of the adjusting
pins recede into the adjusting
lock screws and worn parts
replaced.
Rotor Brake Panel Package
This package consists of
valve, pressure reducer, and
nut 1/8 inch. Replace
each time linings are
an accumulator, relief
a shuttle valve. The
package receives hydraulic pressure from the master
brake cylinder during manual operation. It receives
pressure from the automatic blade folding system
during automatic operation. When the master brake
cylinder handle is in the OFF or DETENT position,
the master cylinder vents to the utility fluid tank.
Movement of the master brake cylinder handle blocks
10-13
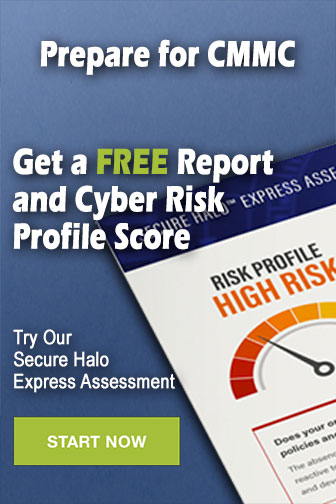