Figure 6-5.Standard tube cutter.
FABRICATION
Fabrication of tube assemblies consists of tube
cuttings, deburring, bending, and tube joint
preparation. The procedures found in this chapter are
for instructional purposes only. When fabricating
tube assemblies, refer to the Aviation Hose and Tube
Manual, NA01-1A-20.
TUBE CUTTING
When you cut tubing, the objective is to produce a
square end free from burrs. Tubing should be cut with
a standard tube cutter, or the Permaswage chipless
cutter.
Standard Tube Cutter
Place the tube in cutter with cutting wheel at the
point where the cut is to be made. Apply light
pressure on tube by tightening adjusting knob. Too
much pressure applied to the cutting wheel at one time
may deform the tubing or cause excessive burrs.
Rotate the cutter toward its open side (fig. 6-5). As
the cutter is rotated, adjust the tightening knob after
each complete turn to maintain light pressure on the
cutting wheel.
Permaswage Chipless Cutter
Select the chipless cutter according to tubing size.
Rotate cutter head to accept tubing in cutting position.
Check to ensure the cutter ratchet is operating freely
and the cutter wheel is clear of the cutter head opening
(fig. 6-6).
Center the tubing on two rollers and cutting blade.
Use the hex key provided with the kit to turn the drive
screw in until the cutter wheel touches the tube.
Tighten the drive screw one-eighth to one-fourth turn.
Do not overtighten the drive screw. Overtightening
can damage soft tubing or cause excessive wear or
breakage of the cutter wheel in hard tubing. Swing
ratchet handle back and forth through the available
clearance until there is a noticeable ease of rotation.
Avoid side force on cutter handle. Side force will
cause the cutter wheel to break. Tighten the drive
screw an additional one-eighth to one-fourth turn, and
swing ratchet handle back and forth, retightening
drive screw as needed until cut is completed.
Figure 6-6.Permaswage chipless cutter.
6-8
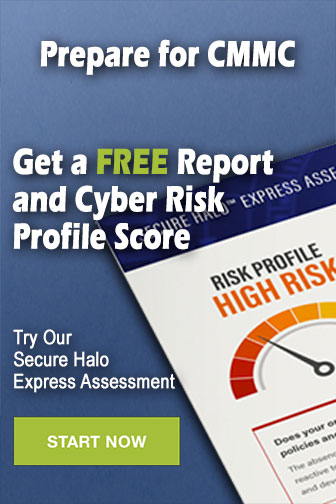