16 psi, it overcomes the spring and opens the cyclic
valve.
Wing and Empennage Deice
Timing Controller
The timing controller is located in the left load
center. This device collects logic information
necessary to provide control signals to the cyclic
valves through solid-state sequence switching. The
controller provides 30-second sequential control
signals to each cyclic valve. It also receives the
60° temperature sensor indication and interrupts
the valve-open cycle when aircraft skin and
structural temperatures exceed 60°±3°F
(15°±1.6°C). The timing controller collects logic
signals to control deice operations in various
failure modes.
Probe Sensor Temperature Transmitter
The temperature sensor is a solid-state
semiconductor thermistor whose resistance varies
with temperature. There are eight temperature
sensors, positioned just inside wing and horizontal
stabilizers leading edge skins. Each is located to
correspond to one of the eight deice piccolo tubes.
When a leading edge skin temperature reaches
60°± 3°F, an electrical signal, furnished by a
temperature sensor to the timing control,
interrupts the operating sequence of the related
cyclic valve. Deice air to the particular piccolo
tube sensed by that temperature sensor is shut
off.
Deice Thermostatic Switch
The thermostatic switch consists of a con-
ventional bimetallic element that closes at a
temperature of 200°±5°F (93°±2°C). Eight
thermostatic switches, mounted on structural
components away from the piccolo tube outlets,
detect possible overheating of area structures. Any
thermostatic switch closure causes the DEICE
HOT warning indicator light on the annunciator
panel to come on, but it does not disable a deice
component.
ENGINE ANTI-ICING SYSTEM
A typical aircraft engine anti-icing system is
designed to allow hot 14th stage bleed air to be
distributed to portions of the engine to prevent
the formation of ice.
The S-3 engine anti-icing system, shown in fig.
1-11, is controlled by a solenoid-operated anti-
icing valve actuated by the anti-icing switch
on the environmental control panel. The
anti-icing valve opens when electrical power is
removed. A pressure switch, located on the anti-
icing valve, senses pressure downstream from the
valve, closes the circuit to the A-ICE ON light
when the anti-icing switch is in ENG & PITOT
(valve open), and opens when the switch is in OFF
(valve closed).
When the anti-icing switch is positioned in
ENG & PITOT, hot 14th stage compressor bleed
air is ducted to the fan nose splitter and air inlet
fairing via the engine nose pylon.
The anti-icing valve regulates the output air
pressure. It includes a backup pressure regulator
in case of failure of the primary element. A pop-
out button on the valve indicates primary pressure
regulating element malfunction.
Air from the anti-icing valve is directed to the
anti-icing discharge manifold where it is split
into two flows. One flow is for engine anti-icing,
the other is directed to the engine air inlet anti-
icing connection.
The engine anti-icing system consists of an
anti-icing valve, anti-icing discharge manifold,
anti-ice external air duct, and a forward anti-ice
duct.
Anti-Icing Valve
The anti-icing valve is a solenoid-operated
valve actuated by the three-position anti-icing
switch. The anti-icing valve is de-energized
open. Failure of electrical power causes the
system to remain in or revert to the anti-icing ON
condition.
Anti-Icing Discharge Manifold
The anti-icing discharge manifold is connected
to the anti-icing valve and provides for the
distribution of the hot 14th stage bleed air
to the air inlet fairing and to portions of the
engine.
1-17
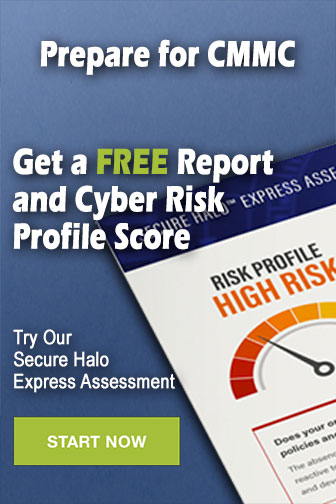