The valve is equipped with a fusible metal
safety plug and a safety disc to release the
contents of the cylinder if the pressure becomes
excessive because of high temperatures. The safety
plug is filled with a fusible metal designed to melt
at temperatures ranging from 208° to 220°F
(97.8° to 104.5°C).
The cylinder and valve assembly is connected
to the oxygen tubing by silver soldering the
tubing to a coupling nose and securing the nose
to the valve outlet with a coupling nut.
The self-opening (automatic) oxygen cylinder
valve is automatically opened when it is connected
to the oxygen line. The use of this type of valve
permits remote location of the oxygen cylinder to
places less vulnerable during combat and more
readily accessible for servicing.
Regulators
The success or failure of high-altitude flight
depends primarily on the proper functioning of
the oxygen breathing regulator. Acting as a meter-
ing device, the regulator is the heart of the
oxygen system. To perform successfully in an air-
craft system, a regulator must deliver the life-
supporting oxygen in the quantities demanded
throughout its entire range of operation.
Although personnel of the PR rating are
primarily responsible for maintenance of
regulators, the AME is responsible for per-
forming operational checks in the aircraft and for
removal and installation. In other words, the
AME removes a malfunctioning regulator from
the aircraft and delivers it to the shop where the
PR determines the trouble and makes the
necessary repairs. When the trouble is corrected,
the AME reinstalls the regulator in the aircraft.
Tubing
Two types of tubing are used in aircraft
oxygen systems. Low-pressure aluminum alloy
tubing is used in lines carrying pressures up to
450 psi. High-pressure copper tubing is used in
lines carrying pressure above 450 psi.
NOTE: Some of the newer naval aircraft are
equipped with high-pressure oxygen lines made
of aluminum alloy.
Lines running from the filler valve to each of
the cylinders are called filler lines. Those
running from the cylinders to the regulators are
called distribution or supply lines.
Oxygen lines, like all other lines in the aircraft,
are identified by strips of colored tape. The strips
of tape are wrapped around each line near each
fitting and at least once in each compartment
through which the line runs. The color code for
oxygen lines is green and white with the words
Breathing Oxygen printed in the green portion,
while black outlines of rectangles appear in the
white portion.
Resistance to fatigue failure is an important
factor in oxygen line design because the line
pressure in a high-pressure system will at times
exceed 1,800 psi, and at other times be as low as
300 psi. Because of these varying pressures and
temperatures, expansion and contraction occur all
the time. These fluctuations cause metal
fatigue, which must be guarded against in both
the design and the construction specifications for
tubing. Steps are taken during installation to
prevent fatigue failure of the tubing. Tubing is
bent in smooth coils wherever it is connected to
an inflexible object, like a cylinder or a regulator.
Every precaution is taken to prevent the accidental
discharge of compressed oxygen because of faulty
tubing or installation. Although simple in con-
struction and purpose, tubing is the primary
means by which oxygen is routed from the
cylinders to the regulator stations.
High-pressure tubing is usually seamless
copper tubing, and is manufactured in accordance
with strict specifications. It has an outside
diameter of 3/16 inch and a wall thickness of
0.035 inch. For application in high-pressure
oxygen installations, copper tubing is type N (soft
annealed), and is pressure tested at not less than
3,000 psi.
High-pressure tubing is used between the
oxygen cylinder valve and the filler connection in
all systems, between the cylinder valve and the
regulator inlet in high-pressure systems, and
between the cylinder valve and pressure reducer
in reduced high-pressure systems.
To connect high-pressure copper tubing,
adapters and fittings are silver soldered to the
tubing ends. Due to the high pressures involved,
the security (leak tightness) of all high-pressure
lines relies primarily on a metal-to-metal contact
of all its fittings and connections. A fitting
properly silver soldered to the end of a length of
copper tubing will not come loose or leak.
Some of the later models of naval aircraft use
aluminum alloy or stainless steel tubing in high-
-pressure oxygen system installations. Replacement
tubing should be manufactured of the same type
4-6
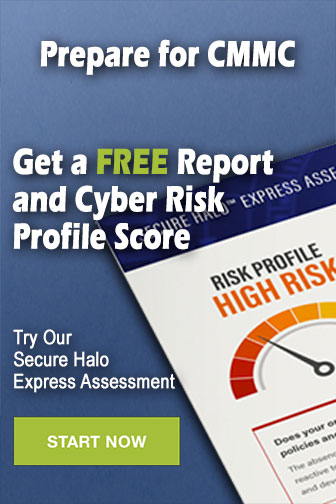