serious threat to flight safety. This program is an
ongoing effort to control hydraulic fluid
contamination.
AIRCRAFT FUEL SURVEILLANCE
PROGRAM
Foreign contaminants and water in aircraft fuel
systems constitute a major hazard in naval aircraft.
Harmful effects of water, particulates, and
microbiological growth include erratic or incorrect
fuel quantity indications; icing of filters, valves, and
other fuel system components; engine failure caused
by carburetor/fuel control icing or malfunction; and jet
engine starting difficulties. Further, if contamination
remains undetected, rubber fuel cells deteriorate and
become permanently damaged. Constant vigilance by
maintenance personnel is required to ensure that clear,
bright, and dry fuel is delivered to the aircraft, and
subsequently to its engines.
All aviation fuels are produced under rigidly
controlled specifications. To maintain its high quality,
maintenance personnel must take careful and
continual measures to prevent contamination.
Contamination can occur from fuel mixing with
other bulk petroleum products as well as from dirt,
rust, and water. Serious engine and airframe problems
develop if inadequate attention and effort are given to
maintaining fuel quality. Since no two fuel systems are
identical, it is not possible to establish rigid and
detailed procedures that will apply in all situations.
The plane captain takes fuel samples from
low-point drains of all fuel cells/tanks before the first
flight of the day. This action is normally accomplished
during the daily inspection. This also includes any
auxiliary, external, or in-flight refueling tanks.
Additional information on this program can be
obtained in the Aircraft Refueling NATOPS Manual,
NAVAIR 00-80T-109.
Q34.
What builds a successful FOD program?
Q35. What officer coordinates the Tool Control
Program?
Q36.
What is the most significant benefit to the Tool
Control Program?
Q37. What is the prime objective of the hydraulic
contamination control program?
Q38.
What publication contains detailed information
on the Aircraft Fuel Surveillance Program?
AVIATORS BREATHING
OXYGEN (ABO) SURVEILLANCE
PROGRAM
Aviators breathing oxygen (ABO) comes in both
gaseous and liquid states. Liquid oxygen (LOX) is
converted to a gaseous state before its delivery to the
aircrew. Because oxygen can be contaminated easily,
LOX requires frequent and continual monitoring by
personnel to ensure detection of contamination. The
safety of the aircrew is of the utmost priority.
An oxygen surveillance program is the primary
method of ensuring that each operation in the LOX
supply system is carried out in strict compliance with
established procedures. Surveillance begins with
procurement or generation of LOX and continues
throughout storage, handling, transfer, and servicing
in the aircraft. This program is also applicable to all
naval activities involved in the support and
manufacture of LOX and related equipment.
Each person associated with the Aviation
Breathing Oxygen Surveillance and Contamination
Program should have a thorough knowledge of the
characteristics of liquid oxygen and gaseous oxygen
and the hazards of contamination. Each person should
also know the quality standards listed in the ABO
Surveillance Program Laboratory Manual and Field
Guide, A6-332A0-GYD-000.
EGRESS SYSTEM CHECKOUT
PROGRAM
The high-performance aircraft used by the Navy
places extreme demands on emergency escape
systems. These systems contain high-explosive
devices that are designed for onetime use only.
Actuation of these devices could result in severe injury
or death to personnel and damage to or destruction of
aircraft. Therefore, because of the inherent dangers
associated with ejection seats and canopy systems, an
egress systems checkout procedure is required.
The egress/environmental work center (AME
shop) indoctrinates all personnel in the hazards and
safety precautions associated with these systems. A
system checkout must be given by a qualified AME to
all new maintenance personnel before they perform
any aircraft maintenance work. Maintenance
personnel must be checked out every 6 months
thereafter before the last day of the requalification
month. In addition, any personnel removed from
aircraft maintenance responsibilities for more than 90
5-27
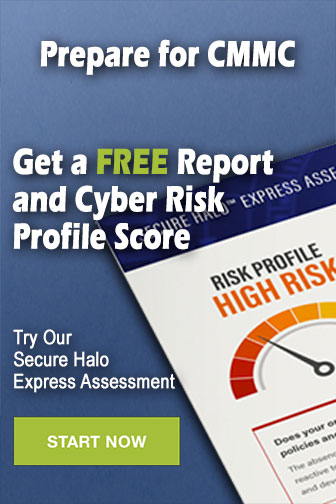