RECTYP 79 data by message in the format that is
outlined in the NAMP. The RECTYP 79 message has
the same submission deadline as RECTYP 79 data that
is submitted by a DSF.
Q18. What material condition describes an aircraft
that is not capable of performing any of its
intended missions due to a lack of parts or
materials?
AIRCRAFT MATERIAL READINESS
REPORT (AMRR)
The aircraft material readiness report (AMRR)
enables supporting commanders (ACCs and type
commanders [TYCOMs]) to assess current aircraft
material condition and identify aircraft support
deficiencies. Preparation of the AMRR is normally a
joint project between personnel in the squadrons,
supply department, AIMD, and carrier air group
(CAG). Usually a worksheet is prepared each morning
by Maintenance Control Personnel and submitted to
either the wing or CAG. The wing or CAG will
incorporate the data of all applicable squadrons and
submit the information by a message to higher
authority. An understanding of the content of the
AMRR should enable you to understand the
relationship between maintenance and supply and how
this relationship impacts total unit readiness.
The AMRR allows ACCs and TYCOMs to readily
identify problem areas (maintenance and supply
related) that hurt an aviation activitys ability to
perform its assigned mission. ACCs and TYCOMs can
then provide assistance to correct the deficiencies.
When an airwing is deployed, the AMRR should be
submitted daily by unclassified message for the entire
airwing and should reflect the status as of the first
flight of the day or 1200 local time, whichever comes
first. Aircraft Material Readiness Reporting,
COMNAVAIRLANTINST/COMNAVAIRPACINST
5442.5, outlines reporting procedures for submission of
the AMRR. The AMRR includes the following
information:
Physical location of the ship and the next port
arrival date
Number and types of aircraft that are assigned to
the airwing
Number of aircraft that are temporarily assigned
ashore
Number of MC and FMC aircraft onboard
Sorties (flights) that were scheduled and sorties
that were flown
Flight hours that were flown since last report
Number of NMCS and NMCM as well as PMCS
and PMCM aircraft
Significant maintenance or support problems
that affect unit readiness
NAVY OIL ANALYSIS PROGRAM
The Navy Oil Analysis Program (NOAP) is used to
monitor and diagnose the condition of equipment or oil
without the removal or extensive disassembly of the
equipment. Activities that operate aeronautical
equipment must participate in the NOAP. Maintenance
requirements cards (MRCs) and maintenance
instruction manuals (MIMs), provided by the cognizant
field activity (CFA), furnish information on oil
sampling. For information on the NOAP, you should
refer to the Navy Oil Analysis Program, OPNAVINST
4731.1. OPNAVINST 4731.1 covers the Joint Oil
Analysis Program (JOAP) and its interrelationship with
the Army, Air Force, and other activities. Operating
procedures are outlined in the Joint Oil Analysis
Program Laboratory Manual, NAVAIR 17-15-50.
Additional information about the NOAP can found in
the NAMP.
Operating activities schedule routine oil sampling
according to the information that is contained in the
MRCs. Special oil samples are submitted to the
laboratory when such samples are required by
NAVAIR 17-15-50. Special oil sampling should be
accomplished whenever the following occurs:
Whenever requested by the JOAP laboratory or
the CFA
Whenever directed by the unit maintenance
activity to check out suspected deficiencies
Immediately before and after maintenance that
affects the oil lubricating system, which
includes removal and replacement of an
oil-lubricated system component
Before and after a test cell run
After the flight test that follows the installation
of a new, repaired, or overhauled engine
Immediately following an aircraft incident that
involves failure of internally enclosed lubricated
5-36
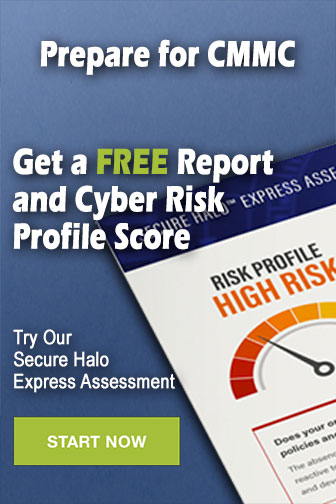