engine(s) is (are) operating and the aircraft is to be
immediately relaunched.
I-LEVEL MAINTENANCEMaintenance which is
the responsibility of, and is performed by,
designated maintenance activities for direct
support of using organizations. Its phases normally
consist of calibration, repair or replacement of
damaged or unserviceable parts, components, or
assemblies; the emergency manufacture of
nonavailable parts; and the provision of technical
assistance to using organizations.
ICAPSIncreased Capabilities SystemICAPS is a
database management system that provides users
with a quick and accurate means to process, store,
and retrieve information on cartridges for CADs.
ICPInventory Control PointAn organizational
unit or activity within a DOD supply system. It is
assigned the primary responsibility for the material
management of a group of items either for a
particular service or for the DOD as a whole.
Material inventory management includes
cataloging directions, requirements computation,
procurement direction, distribution management,
disposal direction, and general rebuild direction.
IDInterface Device or Identification.
IFARS Individual Flight Activity Reporting System.
IMAIntermediate (I-Level) Maintenance Activity
An aviation activity (ship or station) authorized to
provide I-level maintenance support. It consists of
the aircraft maintenance, supply, and weapons
departments/divisions.
IMIInteractive Multimedia Instruction.
IMRLIndividual Material Readiness ListA
consolidated list shows items and quantities of
certain SE required for material readiness of the
aircraft ground activity to which the list applies.
The lists are constructed by extracting those
portions of SERMIS that pertain to the
maintenance and material logistics responsibilities
of the activity to which the list applies.
IN MCRSIn Material Condition Reporting
StatusThe term (inventory code A) means that an
aircraft is in the inventory system and that the
aircraft requires SCIR documentation. IN MCRS is
the normal status of aircraft.
INCIncorporated.
IN-SHOP MAINTENANCEWork that requires the
use of shop facilities and cannot be normally
performed outside the shop. (Bench test and
component disassembly and repair are examples. of
in-shop maintenance work.)
INITIAL OUTFITTINGThe process of issuing,
assembling, and delivering allowances of
aeronautical material and equipment to vessels in
any one of the following categories: (1) new
construction, (2) conversion, or (3) activating from
reserve fleets.
INSPECTTo compare the characteristics of an item
with established standards.
INSPECTIONThe examination and testing of
supplies and services, including raw materials,
components, and intermediate assemblies, to
determine whether they conform to specified
requirements.
INSPECTIONS, AIRCRAFT/ENGINE
ACCEPTANCE INSPECTION
CONDITIONAL INSPECTION
DAILY INSPECTION
MAJOR ENGINE INSPECTION
PHASE INSPECTION
SPECIAL INSPECTION
TRANSFER INSPECTION
TURNAROUND INSPECTION
ZONAL INSPECTION
INSPECTIONS, SE
ACCEPTANCE INSPECTION (SE)
PERIODIC INSPECTION
PREOPERATIONAL INSPECTION
TRANSFER INSPECTION (SE)
ZONAL INSPECTION
INSTRUCTIONSDirectives of a continuing nature
that are effective until subsequently canceled.
Instructions use a subject classification numbering
system per the Navy directives system.
INTERCHANGEABLE ITEMSTwo or more
items that have such functional and physical
characteristics as to be equivalent in performance
and durability and are capable of being
interchanged without alteration of the items
themselves or of adjoining items except for
adjustment.
AI-11
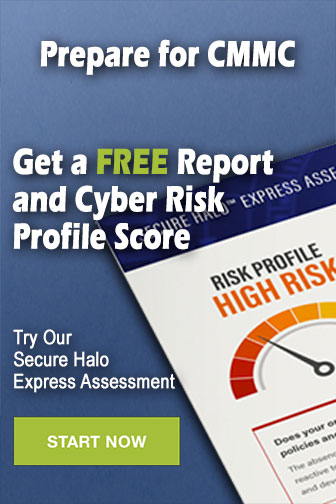