CHAPTER 5
MAINTENANCE DATA SYSTEM (MDS)
An AZ who works in maintenance control or
production control should have a working knowledge
of the Maintenance Data System (MDS). Maintenance
controllers initiate and complete much of the data that
is generated through the MDS. As a maintenance or
production controller, you might be called upon to
research and extract critical information about
aeronautical equipment from the Naval Aviation
Logistics Command Management Information System
(NALCOMIS), data services facility (DSF)
machine-produced maintenance data reports, or
maintenance or flight data historical files. A working
knowledge of MDS procedures and available MDS
products should prevent a simple search for needed
data from becoming a lengthy evolution. At any rate,
the most important thing you should remember is that
the information taken from MDS is only as good as the
information put into MDS. Accuracy in MDS
documentation should be your primary concern.
MAINTENANCE DATA SYSTEM
SCOPE
LEARNING OBJECTIVE: Define the
function of the Maintenance Data System
(MDS).
The MDS is a management information system
provides statistical data on aeronautical equipment for
use at all management levels. This statistical data is
concerned with:
Equipment maintainability and reliability
Equipment configuration
Equipment mission capability and utilization
Material usage
Material nonavailability
Maintenance and material processing times
Weapon system maintenance and material cost
MDS also assists maintenance managers in the
day-to-day management of the maintenance effort. The
key ingredient to an effective MDS in a maintenance
activity is the work center supervisor. Work center
supervisors should have a working knowledge of the
MDS, the proper use and documentation of source
documents, and knowledge of the available content of
machine reports. The sources of much of the data that is
generated in the MDS include the maintenance action
form (MAF), the naval aircraft flight record
(NAVFLIR), and the MILSTRIP Requisition Form,
DD Form 1348. These source documents are the tools
that are used to collect, record, and report the
information that is needed for the efficient and
economical management of maintenance, material and
manpower.
In the following pages, we will discuss three of the
four reporting subsystems that make up the
MDSmaterial reporting (MR), maintenance data
reporting (MDR), and subsystem capability impact
reporting (SCIR). A fourth subsystem, utilization
reporting, is not dealt with here.
Q1.
What management information system is
designed to provide statistical data on
aeronautical equipment for use at all
maintenance levels?
MATERIAL REPORTING
(MR)
LEARNING OBJECTIVE: Define the
purpose of Material Reporting.
The Material Reporting (MR) subsystem reports all
supply actions that support aviation maintenance.
Using the MAF, material requisition (DD Form 1348),
and NALCOMIS as its sources of information, the local
supply organization submits repairable component
control data and usage data to the supporting DSF. The
DSF produces reports from the data that merge key
elements of maintenance and supply. These reports
provide local supply and aviation intermediate
maintenance departments (AIMDs) with a means to
monitor the flow of repairable components. The reports
also provide management at higher commands with
information on the material expenditures that are used
in support of maintenance.
5-1
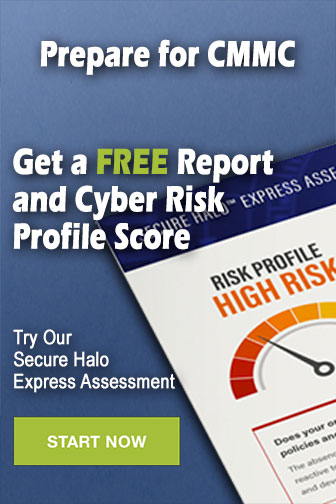