MR is a part of the MDS; however, the primary
responsibilities for the detailed procedures that are
involved in MR are NOT the direct responsibility of the
AZ. Therefore, MR will not be discussed further.
Q2. What reporting system is used to report all supply
actions that support aircraft maintenance?
MAINTENANCE DATA REPORTING
(MDR)
LEARNING OBJECTIVES: Define the
purpose of Maintenance Data Reporting.
Identify the purpose of various Maintenance
Data Reports. Identify the purpose of selected
NALCOMIS reports.
MDR deals with the most complex and the widest
range of data in the MDS. Maintenance data is
generated at the most basic levelfrom the mechanic
or technician who performs the maintenance task.
Source documents that are used in maintenance data
reporting include the MAF and the Metrology
Equipment Recall (METER) card. By using coded
information that is documented on these source
documents, the local DSF compiles maintenance and
material data reports. Aircraft maintenance workers use
source documents to report the following information:
What equipment was worked on (which system,
subsystem, or component)
What caused the failure or malfunction
When the failure or malfunction was discovered
What action was taken to repair the equipment
What parts were used to repair the equipment
The number of man-hours that were expended in
repair
The identity of the work center or work centers
that did the work
Once this information is compiled in a useable format
(for example, monthly maintenance summaries),
maintenance managers can use the information to
manage aircraft maintenance organizations.
MAINTENANCE DATA REPORTS
Maintenance technicians at the local level generate
large amounts of maintenance data. This data consists
This MAF copy 1 DAR is prepared from data that
was submitted on MAFs and is compiled in three parts.
Part I and Part II are shown in figure 5-1. Part I contains
data that have no errors, and each data element is
considered valid. Part II contains records for the current
reporting period that contain errors that have not been
previously corrected. Part III will be produced only if
there are correction or deletion records that cannot be
applied to the local database due to erroneous data. In
part III, an asterisk (*) indicates erroneous data. When
erroneous data is indicated, the work center supervisor
should verify the MAF copy 1 daily audit report to
ensure that data that is contained on production work
center MAFs has been correctly processed by the
DSF.
Monthly Production Report (MDR-2)
The MDR-2, shown in figure 5-2, lists all
maintenance actions in work center sequence, which
includes technical directive compliance and data that
has been entered in the (H-Z) Failed/Required Material
blocks of the MAF. The MDR-2 also provides the work
center supervisor with statistical data that pertains to
the work center, for example, man-hours that were
expended in repair of a subsystem.
5-3
Job Control Number (JCN) Consolidation
Report (MDR-3)
The MDR-3 (fig. 5-3) is a consolidated list of all
maintenance and technical directive compliance
actions that were submitted during the month by the
parent organization and the supporting activity. This
report is prepared from data on all MAFs except those
with transaction codes 00, 02, and 03 (inventory gain,
change in material condition reporting status, and
inventory loss). The MDR-3 gives the maintenance
officer (MO) a record of maintenance on the equipment
for which he or she is responsible.
of coded elements that the DSF summarizes into daily
and monthly reports. For a detailed description and
examples of MDS reports, refer to the Naval Avia-
tion Maintenance Program (NAMP), OPNAV-
INST 4790.2. Some of the DSF-generated MDS that
we will discuss are available in both organizational-
and intermediate-level maintenance activities.
MAF Copy 1 Daily Audit Report (DAR)
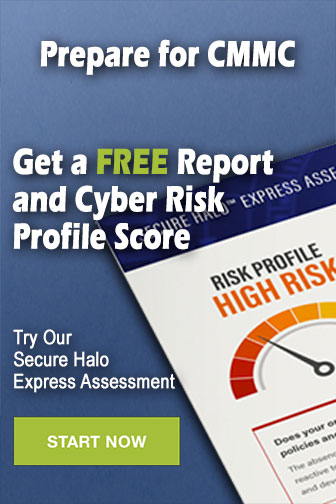