No Defect Report (MDR-12)
The MDR-12, shown in figure 5-12, shows the
amount of time and effort that were expended on
maintenance for which there is no malfunction. This
report is used to determine man-hours that were
expended in removing or installing items with no
known malfunction or defect to carry out other
maintenance.
When Malfunction Was Discovered Report
(MDR-13)
The MDR-13, shown in figure 5-13, shows the
action taken by category for each When Discovered
code. This report is prepared from data that was
submitted on the METER card and the MAF. The MO
can use the MDR-13 to determine how many missions
were aborted due to mechanical failures, what caused
them, whether these malfunctions were discovered
before flight or while in flight, and whether the
malfunctions could have been eliminated by better
inspections of the aircraft.
NALCOMIS PRODUCTION REPORTS
MDRs are prepared monthly by DSFs for aviation
maintenance activities; however, maintenance
managers (MOs, MMCOs, maintenance control
officers, maintenance chiefs, and so forth) need
maintenance and supply data to make decisions about
the day-to-day maintenance effort. NALCOMIS fills
this need. NALCOMIS provides a Reports Subsystem
Menu from which maintenance managers can generate
daily maintenance, material, and flight data reports. For
a complete description and list of available
NALCOMIS reports, refer to the NALCOMIS OMA
End Users Manual, section 10. Below is a list of
selected maintenance reports available to a
maintenance activity through NALCOMIS:
Aircraft Daily Status Reportprovides data
on each aircraft that is assigned to your activity
Aircraft/Equipment Workload Reportlists
outstanding MAFs on a specific aircraft or
equipment
Scheduled Inspections Reportlists sched-
uled aircraft inspections and inspections due
dates
Inspections by Type Equipment Code
(TEC)lists inspections that have been
established for each type equipment code (TEC)
Aircraft Phase Inspection Reportlists hours
that remain until phase inspections are required
for assigned aircraft
Aircraft Material Status Reportlists the
status of material status requisitions against
aircraft that are assigned to your activity
Q3. What MDS reporting subsystem involves the most
complex and widest range of data in the MDS?
Q4. What maintenance data report is divided into
three sections, contains data in Part I that has no
errors, and is considered valid?
Q5. What maintenance data report is a detailed list of
technical directive compliance during a reporting
period?
Q6. What NALCOMIS report provides a listing of all
outstanding MAFs for a specific aircraft or
equipment?
SUBSYSTEM CAPABILITY IMPACT
REPORTING (SCIR)
LEARNING OBJECTIVES: Define Sub-
system Capability Impact Reporting (SCIR).
Identify terms and codes that are used in
aircraft and equipment inventory reporting.
Identify the purpose of the Equipment Master
Roster (E-00). Identify the purpose and content
of SCIR reports.
The supporting DSF produces SCIR reports from
data, which is documented on the MAF, to provide
information about aircraft and equipment inventory,
subsystem performance, and specific aircraft or
equipment mission capability. SCIR also tracks full
mission capable (FMC), partial mission capable
(PMC), and not mission capable (NMC) data for
specific type and model aircraft or equipment. In
addition, SCIR tracks certain training devices.
Management above an aviation maintenance activity
level use SCIR reports to oversee mission capability of
the activity.
An aviation maintenance activity reports the
degradation of equipment mission capability by
recording an equipment operational capability (EOC)
code in the Repair Cycle section and in the
Maintenance/Supply Record section of a MAF. An
EOC code is a three-position code that documents
when a discrepancy in a specific system or subsystem
impacts the mission capability of an equipment. The
maintenance activity documents the first position of the
5-17
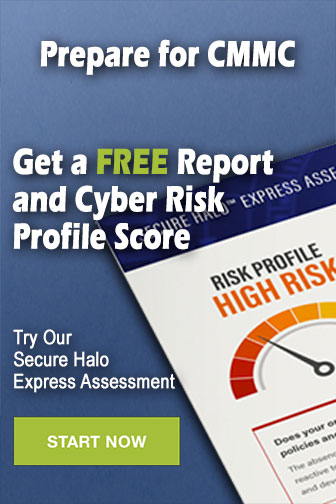