CHAPTER 7
MAINTENANCE PLANNING AND ADMINISTRATION
As the workcenter or branch supervisor, you are
directly responsible for the maintenance effort of your
workcenter. The planning, scheduling, control and
parts ordering are essential to its accomplishment.
The factors that you must consider in maintenance
planning
are
equipment
status,
operational
requirements, the workload, and the personnel assets
available to perform the job.
PLANNED MAINTENANCE SYSTEM
LEARNING OBJECTIVES: State who has
the responsibility for managing PMS programs
for equipment aboard ship. Identify three
considerations
used
to
determine
PMS
procedures.
The Planned Maintenance System (PMS) is a
simplified, yet thorough means of accomplishing
preventive maintenance aboard ship. It identifies
maintenance requirements, and schedules maintenance
actions to make the best use of your resources. It
increases economy and simplifies records. It improves
management,
workload
planning,
equipment
reliability,
and
on-the-job
training
of
shipboard
personnel. As a system, however, it is neither
self-starting nor self-sustained, and careful supervision
at all levels is required.
PMS procedures and how frequently the actions
should be done are developed for each piece of
equipment based on good engineering practices,
practical experience, and technical standards. These
step-by-step procedures are published on maintenance
requirement cards (MRCs). The cards contain detailed
information on each maintenance requirement, such as
who (specific rate) should perform the maintenance,
and when, how, and with what resources. Some MRCs
have equipment guide lists (EGLs) to identify the
locations of various pieces of the same type of
equipment, such as motors, controllers, valves, life
rafts, deck fittings, and hatches that are serviced at the
same time.
Keep in mind that PMS actions, as preventive
maintenance actions, are the minimum maintenance
actions required to maintain the equipment in a fully
operable condition. If PMS actions are performed
according to schedule, they will allow equipment
operators and maintenance personnel to identify
possible problems before equipment failure. Properly
performed PMS actions will help prevent failures that
could result in repeated corrective maintenance actions.
PMS procedures are developed by the activities and
offices of the systems commands responsible for the
development and procurement of the systems and
equipment they control. PMS maintenance index pages
(MIPs) and MRCs are developed as part of the
Integrated Logistics Support effort for all new
procurements,
alterations,
and
modifications
of
systems and equipment.
Management tools provided by PMS for each ship,
department, and supervisor include the following:
Comprehensive procedures for planned main-
tenance of systems and equipment
Minimum requirements for planned main-
tenance
Scheduling and control of maintenance
Description of the methods, materials, tools, and
personnel needed to perform maintenance
Prevention or detection of hidden failures or
malfunctions
Test procedures to determine material readiness
PMS, though standard in concept and procedures,
is flexible enough to be adjusted by the ship to be
compatible with operational and other types of
schedules.
DEPARTMENTAL MASTER PMS MANUAL
A Departmental Master PMS Manual is maintained
in each departmental office for use in planning,
scheduling, and supervising required maintenance. The
information contained in this manual pertains only to
equipment for which the department is responsible. The
Departmental Master PMS Manual contains the
following:
1.
Supplementary
Information:
Additional
instructions, information, and data provided to
7-1
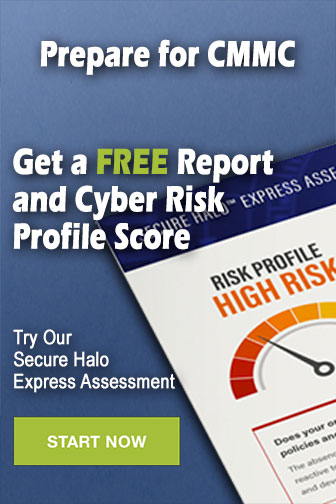