system (fig. 3-3) to rotate the CROV cam. Rotation of
this cam forces a plunger down onto a set of levers (fig.
3-4), which in turn forces a valve sleeve and valve stem
down to mate with a valve seat to close the valve,
shutting off the flow of fluid from the engine cylinder to
the engine accumulator, bringing the aircraft to a stop.
As stated earlier, the CROV is designed to bring all
aircraft, regardless of weight, to a controlled stop while
using approximately the same amount of flight deck
landing area. This is accomplished by adjusting the
allowable opening of the CROV, a smaller, more
restrictive opening to arrest a heavy aircraft or a large
valve opening to arrest a light aircraft.
CONSTANT RUNOUT VALVE (CROV)
WEIGHT SELECTOR
The aircraft weight selector makes it possible to
adjust the CROV for aircraft of different weights by
varying the valve opening. See figure 3-4.
The size of the initial valve opening is adjusted
while the arresting engine is in the BATTERY position.
The lead screw receives rotary motion from the motor
unit or handwheel and converts it into linear motion.
This linear motion positions the upper lever and drives
the local and remote indicators.
In each of the two levers (upper and lower), the
distance between the fulcrum and roller is constant. On
the upper lever, the distance between the fulcrum and
the point of application of force from the cam is
variable, its greatest length being twice that of the lower
lever. The lever arm ratio of each lever, therefore, is
variable between 1:1 and 2:1.
When the upper lever is fully extended, the ratio of
each lever is 1:1. In this setting the initial opening of the
control valve upon engagement of an aircraft is
maximum. The resulting rotation of the cam, caused by
the crosshead moving inward, forces the plunger
downward. A plunger movement of 1 inch, acting
through the upper lever, would move the lower lever 1
inch; the lower lever, in turn, would move the valve
sleeve and stem 1 inch downward.
The cam is a disc plate type with the desired
contour machined on its periphery. As the cam rotates,
it forces the plunger down. The plunger is fitted with
rollers, top and bottom.
The bottom roller on the plunger acts against the
top flat bearing surface of the upper lever. The pivot end
of the upper lever has a bushed hole that mates with the
clevis end of the lead screw yoke. The upper lever is
connected to the clevis end of the yoke by a pin. This
pin extends beyond the sides of the yoke and acts as a
shaft and has a bushed roller mounted on each extended
end. The rollers ride inside the guide attached to the
housing. The block end of the yoke is connected to the
lead screw by two dowel pins. This connection provides
the means by which the lead screw adjusts (moves) the
upper lever.
3-6
INDICATOR PLATE
CONTROL
VALVE
CAM
RAM TRAVEL
AND DECK
RUNOUT DIAL
CONTROL VALVE
REF (CROV)
DRIVE
CHAINS
PULLEY
PULLEYS
CONTROL VALVE
DRIVE CABLE
MOVEABLE CROSSHEAD
PULLEYS
ADJUSTABLE
ANCHOR
ABE3f0303
Figure 3-3.Constant runout valve drive system.
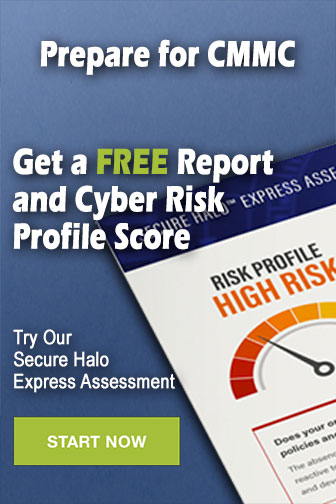