Prior to commencing aircraft recovery operations,
the following considerations apply:
All arresting gear equipment is in normal operating
condition and all Maintenance Requirement Cards
(MRCs) preoperational requirements have been met.
All personnel involved in recovery operations have
completed the applicable Personnel Qualification
Standards (PQS) and are fully qualified to perform their
assigned tasks. Personnel not yet qualified may be
utilized, but only if under the direct supervision of a
fully PQS qualified crewmember.
EMERGENCY RECOVERY OPERATIONS
An emergency arrestment is accomplished in the
same manner as a normal arrestment except that a
barricade webbing assembly transmits the aircraft's
landing force to the purchase cable instead of a
crossdeck pendant.
ARRESTING ENGINE
LEARNING OBJECTIVE: Describe the
components of the arresting engine.
The Mk 7 arresting engine is a hydropneumatic
system composed of the engine structure, a cylinder
and ram assembly, a crosshead and fixed sheaves, a
control valve system, an accumulator system, air flasks,
and a sheave and cable arrangement.
Improvements are continuously being made to
increase the capabilities of carrier-based aircraft. As the
capabilities of the aircraft are increased, the weight and
speed also increase. Therefore, the equipment used to
recover the aircraft aboard carriers must also be
improved to keep pace with aircraft advancement. Such
improvements
have
brought
about
the
recovery
equipment installed on our carriers in the fleet
todaythe Mk 7 Mod 3.
All pendant and barricade engines are Mk 7 Mod 3,
except the barricade engines installed on CV-64 and
CVN-65, which are Mk 7 Mod 2. For more information
on the Mk 7 Mod 2 refer to Operational and
Organizational/Intermediate Maintenance Manual,
NAVAIR 51-5BBA-2.1 and 2.2. Table 3-1 lists the
leading particulars of the Mk 7 Mod 3 recovery
equipment.
ENGINE STRUCTURE
The engine structure is a framework for supporting
the engine and most of its components and for securing
the entire assembly to the ship's structure. It is
composed of a welded steel base made in two
longitudinal box sections with the necessary ties,
plates, and other structural members. The two sections
are bolted together near the center. See figure 3-1.
Two pairs of saddles are mounted on the base for
supporting the engine cylinder. Vertical stands are
welded on these saddles to support the saddles for the
accumulator. Between these two stands is a frame of
welded channels, angles, and gusset plates to provide
trusses and ties for the frame.
On the crosshead end of the welded base support
plates, webs and gussets support the rails for the
crosshead. On this end of the base are welded
longitudinal guides for the accumulator assembly. Near
the end of this frame and bolted to it is the crosshead
stop, which is removed when the crosshead is installed
or removed.
CONSTANT RUNOUT VALVE (CROV)
ASSEMBLY
The constant runout valve (CROV) is installed at
the fixed sheave end of the Mk 7 arresting engine, as
illustrated in figure 3-1. It is designed to stop all aircraft
with the same amount of runout regardless of the
aircraft's weight and speed (within the limits specified
in current recovery bulletins).
The CROV is the heart of the equipment. It controls
the flow of fluid from the cylinder of the arresting
engine to the accumulator. The other components of the
valve are used either to adjust the initial opening of this
valve for aircraft of different weight or to activate the
valve during the arresting stroke.
CONSTANT RUNOUT VALVE (CROV) DRIVE
SYSTEM
When a landing aircraft engages a deck pendant, or
barricade, it withdraws purchase cable from the arrest-
ing engine. This action causes the crosshead to move
toward the fixed sheave end of the engine. In addition to
causing fluid displacement from the engine cylinder,
the movement of the crosshead causes the CROV drive
3-4
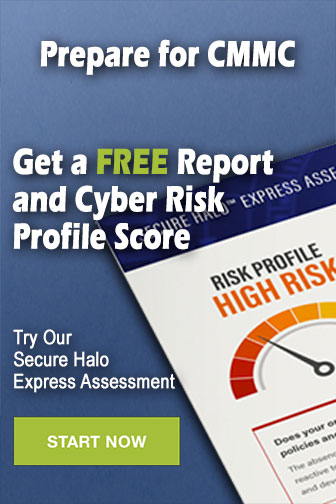