controlling custodian. The 3M Aviation Organization
Code Master Listing, NAMSO 4790.A7065-01,
provides a complete listing of these codes. The first
character of the organization code identifies the major
command. The second and third characters identify
specific units within the major command. Refer to the
NAMP, volume V, appendix K for more information on
organization code structuring.
. Enter the JOB CONTROL NUMBER (JCN) in
the register. The JCN is a 9-, 10-, or 11-character
alphanumeric code that serves as the base for the
maintenance data report (MDR) and control procedures.
The JCN allows for separate identification of each
maintenance action. Also, it provides a link with the
maintenance actions performed by the intermediate
maintenance activity (IMA) in support of an activity or
an O-level maintenance discrepancy. The JCN consists
of four parts. They are the organization code, date, serial
number, and suffix. The paragraph above describes the
organization code. The date is the last three digits of the
Julian date. This is the date the JCN was assigned to a
maintenance action. It does not necessarily reflect the
date when the work started. The serial number maybe
a three-digit number that runs sequentially from 001 to
999. Also, it maybe three alphanumeric characters. This
number is used in sequence for each new job initiated.
After using serial 999, the next number in sequence will
be 001. The alphanumeric characters are used only when
documenting inspections other than preflight,
postflight, turnaround, daily, special, conditional,
corrosion, and acceptance/transfer. This element may be
omitted for initial issues and issues from pre-expended
bins.
. Enter the TYPE EQUIPMENT CODE (TEC)
that describes the end item on which the work is being
performed. This is a four-character code that identifies
the end item or category of equipment. Refer to the
NAMP, volume V, appendix Q, for additional
information about this code.
. Enter the BUREAU or SERIAL NUMBER of
the equipment or item being worked on. If the number
is more than six digits, enter the last six. If it is less than
six digits, prefix it with zeros to make six digits. This
element maybe omitted, if not applicable.
. Enter the WORK UNIT CODE (WUC) that
identifies the system, subsystem, or component. Refer
to the WUC manual for specific aircraft type. The
NAMP, volume V, appendix O, provides a list of general
WUC. This element may be omitted for issues on
technical directive compliance (RECTYP 64). Also, this
element may be omitted for initial issues and issues from
pre-expended bins.
l Enter the COMMERCIAL AND GOVER-
NMENT ENTITY (CAGE) code. This element must
contain the engine TEC in lieu of the CAGE when
ordering engines. Cognizance symbol 4V identities
engines.
. Enter the PART NUMBER of the required item.
. Enter the QUANTITY needed to do the work
. Enter the PROJECT CODE assigned. NAVSUP
P-437 and P-485 provide a list of project codes.
. Enter the proper REQUISITION PRIORITY
DESIGNATOR according to OPNAVINST 4614.1
(series).
. When required,
enter the REQUIRED
DELIVERY DATE (RDD).
. When needed, enter the DELIVERY POINT.
. Enter the ADVICE CODE when needed. An
advice code is mandatory for repairable items.
. Enter the DOCUMENT NUMBER assigned
from the requisition log.
Material for technical directive (TD) modifications
are issued and accounted for based on the requirements
stated on the TD.TD kits and government-furnished
equipment (GFE) that complements these kits are
budgeted and issued as NAVAIR-owned material. They
are issued for onetime installation in specified
equipment during fleet maintenance overhaul, repair, or
modification programs. The Naval Aviation
Maintenance Office (NAMO) assigns the kit
identification numbers for TD kits and GFE. The
purpose for assigning the kit number is for identifying,
requisitioning, and reporting the items. The Aviation
Supply Office (ASO) maintains the records and stock
balances of the kits for NAMO on the master data file.
The daily receipt and processing of transaction item
reports (TIR) updates the master data file.
If available, use pre-expended bins (PEB) to get the
required items. PEB consist of low-cost, frequently
used, maintenance-related items. Items stocked in the
PEB are already paid for. Issues made from PEB do not
create a charge to a squadrons account. The value of
material in the PEB is charged to the overhead of
industrial-type activities. At other activities, the value is
charged to the accounts chargeable. The purpose of the
PEB is to shorten the issue and accounting procedures
8-3
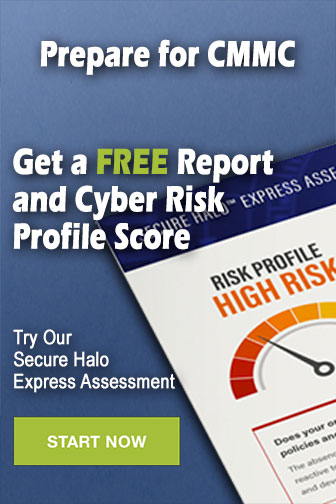