for recurring issues of specific items. The supply
response section (SRS) of ASD manages the PEB. MCC
should review requests for consumable items against the
PEB listing provided by the supporting supply activity.
Requisitioning
In the process of ordering the items needed to
support maintenance, MCC should perform the
following:
l Receive requests from work centers or areas.
l Log requirements in the material control register
or log book.
. Forward requirements to ASD by using
requisition forms or by electronic means. Ensure the
data on requisitions are correct. Refer to chapter 4 of this
manual for requisitioning procedures.
For activities using NALCOMIS, submit requisi-
tions by using Conversation codes N601 or N602. Use
Conversation code N601 for direct support (MAF-
related) material requirements. Use N602 for indirect
support (not related to MAF) material requirements.
. Enter the date and time in the register or log to
reflect the exact time of submission to ASD. This time
is required for determining the accurate timing for
conducting follow-up inquiries.
When ordering a repairable component, the
defective component must be available for simultaneous
exchange upon delivery of the item. When ASD
personnel pick up the defective component, you should
obtain a signature as proof of turn-in.
Field-level repairable with assigned SM&R code
PAOOO must be processed through the Aeronautical
Material Screening Unit (AMSU) for disposition. The
AMSU is part of the maintenance department.
In some instances, it is not feasible or advisable to
remove repairable components until a replacement is in
hand. The Consolidated Remain-In-Place List (CRIPL)
identifies those items included in this group. The items
listed in the CRIPL are the only authorized exceptions
to the one-for-one exchange rule. OPNAVINST
4440.25 (series) describes the responsibilities and
procedures for establishing, maintaining, and modifying
the CRIPL.
Establishment of phase maintenance kits is optional
as directed by the aircraft controlling custodian (ACC)
or type commander (TYCOM). When the program is
implemented, the following procedures apply.
l Maintenance and material control officers jointly
determine phase maintenance kit requirements. They do
this by using the Maintenance Requirements Cards
(MRC) and other maintenance information.
. Material control prepares and submits a listing of
items included in the phase kits. The listing must have
the part number and quantity of each item in the kit.
Also, the listing must include the support period of the
kit; for example, 30-day maintenance period.
. Material control must tell ASD if the kit requires
replenishment. MCC also must inform ASD about any
changes in part numbers or quantity requirements in the
kit.
l The phase maintenance kits may be pre-
expended or charged to the user upon issue. This is based
upon the total parts inventory cost in each kit.
l Mandatory turn-in repairable components are not
authorized in phase maintenance kits. These are the
depot-level and field-level repairable items.
Requisition Monitoring
Monitoring requisitions is necessary to keep the
outstanding file current. You should monitor
requisitions from the date of submission until receipt of
material. There are options for modifiers, follow-ups,
and cancellations, as well as receipt of status. A
NALCOMIS activity uses Conversation code N668 to
review past and current status of a specific requisition.
The supporting ASD provides a listing of all
outstanding NMCS, PMCS, and ANMCS requisitions
daily. This listing contains the document number, NSN,
unit of issue, quantity, project code, and priority. Also,
it may contain the nomenclature, aircraft bureau
number, requisition status, JCN, and WUC. Listings
may have additional information as set by existing
procedures. You must review this listing with
maintenance control and make changes as necessary.
To effectively monitor the outstanding requisitions,
you must be familiar with set procedures. This includes
procedures for requisition modifiers, follow-up, and
cancellation. Chapter 4 of this manual provides basic
information of the procedures for requisition
monitoring.
Material Obligation Validation
The purpose of the material obligation validation
(MOV) request is to compare records and make sure that
a requirement still exists. Supply activity forwards the
8-4
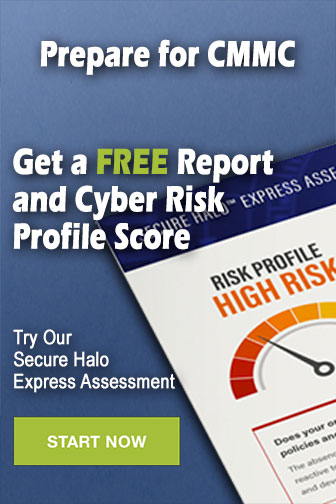