to receive a pivot pin. The pivot pin passes through
the lever and through two mounting holes in the
stanchion.
The bottom of the lower lever is fitted with a
roller that bears on the stem screw on top of the
valve sleeve. The vertical position of the roller on
the lower lever determines the vertical distance that
the valve sleeve may move. Thus, it controls the
size of the initial opening of the control valve.
The levers are mounted in such a way that, as
the upper lever is withdrawn, the lever arm ratio of
both levers is increased by an equal amount. When
the upper lever is fully withdrawn, the ratio of each
lever is 2:1, and the ratio through the lever system
(upper and lower levers) is 4:1. In this case the
initial control valve opening is minimum. A plunger
movement of 1 inch, acting through the upper lever,
would move the lower lever 1/2 inch; the lower
lever, in turn, would move the valve sleeve and stem
1/4 inch downward.
A critical point to consider is the position of the
levers when the valve stem is seated by cam action
at the termination of each arrestment stroke. The
levers are so mounted and adjusted that the bearing
surfaces of the levers are level when the valve is
seated. When the bearing surfaces are level, the
distance across the lever system is the same
regardless of the ratio setting. Because of this, the
point of closing of the valve is independent of the
aircraft weight selector. It is a function of the cam
only; therefore, it is constant.
As the engine is retracted, the upper lever rises
a distance equal to the movement of the plunger.
If the ratio is 1:1, the valve sleeve rises the same
distance.
In this case the initial valve opening is
maximum. If the ratio is 4:1, however, the valve
sleeve rises only one-fourth the distance that the
plunger moves. In this case the initial valve opening
is minimum.
The lever setting may be adjusted to any setting
within the two extremes previously discussed; the
particular setting used is dependent upon the weight
of the aircraft to be arrested. The weight setting is
made with the engine in battery position prior to
landing the aircraft.
Adjustment of the setting determines the
position of the valve sleeve. Therefore, it also sets
the amount the valve will open at the beginning of
the arrestment stroke. Similarly, it determines the
rate of closure during the stroke so that the valve
will always seat at the same runout.
The valve stem sleeve allows a relatively
unloaded and cushioned opening at the beginning of
the stroke.
The lever system, if set for a heavy aircraft,
reduces the allowable valve stem opening and thus
increases the resistance of the valve to the flow of
fluid. The energy of the aircraft is dissipated by
forcing fluid through the restricted valve opening.
Electrical System
The electrical system provides, controls, and
safeguards the distribution of electrical energy to the
weight selector motor and the synchro indicators.
The electrical circuits (fig. 3-5) are the control valve
weight selector circuit and the indicator circuit.
Control Valve Weight Selector Circuit
Due to the varying weights and landing speeds
of carrier-based aircraft, it is necessary to vary the
initial opening of the CRO valve and have a smaller
initial opening for heavier aircraft than for lighter
aircraft. The variation of the setting of the CRO
valve is the function of the aircraft weight selector
motor unit. (See fig. 3-5.) Normally, the settings
are made electrically by depressing an increase or
decrease push button located at the control valve.
The settings can also be accomplished manually by
a handwheel at the control valve.
The aircraft weight selector is motor operated
from the 440-volt, 60-hertz, 3-phase ships power
supply. A fused switch box or breaker is provided
to energize or de-energize the control circuit. To
increase and decrease settings, the direction of the
aircraft weight selector motor rotation is controlled
by the motor controller. Should an electrical failure
occur, the settings can be made manually by pulling
out on the handwheel and turning in either the
increase or the decrease direction.
Settings on the aircraft weight selector are
monitored locally at the control valve motor unit
dial and remotely by synchro receivers located at
Pri-Fly and the deckedge control station.
3-8
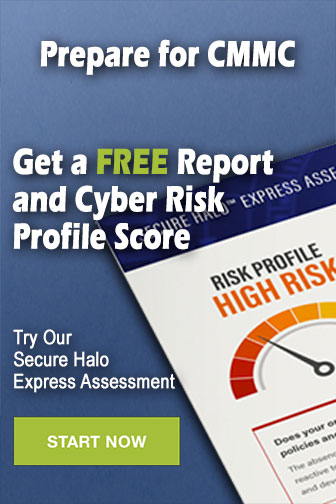