As we continue our discussion on the engine
components and operating procedures in this
chapter, the only reference to the modifications
Mod 2 or Mod 3 will be to point out where a
particular component or operating procedure differs
in one Mod from the other.
Engine Structure
The engine structure is a framework for
supporting the engine and most of its components
and for securing the entire assembly to the ships
structure.
It is composed of a welded steel base
made in two longitudinal box sections with the
necessary ties, plates, and other structural members.
The two sections are bolted together near the
center. See figure 3-1.
Two pairs of saddles are mounted on the base
for supporting the engine cylinder. Vertical stands
are welded on these saddles to support the saddles
for the accumulator. Between these two stands is a
frame of welded channels, angles, and gusset plates
to provide trusses and ties for the frame.
On the crosshead end of the welded base
support plates, webs and gussets support the rails
for the crosshead. On this end of the base are
welded longitudinal guides for the accumulator
assembly. Near the end of this frame and bolted to
it is the crosshead stop, which is removed when the
crosshead is installed or removed.
Constant Runout (CRO)
Control Valve Assembly
The constant runout control valve (CRO valve)
is installed at the fixed sheave end of the Mk 7
arresting engine, as illustrated in figure 3-1.
It is designed to stop all aircraft with the same
amount of runout regardless of the aircrafts weight
and speed (within the limits specified in current
recovery bulletins). The CRO valves of both the
Mk 7 Mod 2 and the Mk 7 Mod 3 arresting engines
have the same major partsarresting valve, aircraft
weight selector, drive system, and control system.
The CRO valve is the heart of the equipment.
It controls the flow of fluid from the cylinder of the
arresting engine to the accumulator. The other
components of the valve are used either to adjust
the initial opening of this valve for aircraft of
different weight or to activate the valve during the
arresting stroke.
The CRO Drive System
When a landing aircraft engages a deck pendant,
or barricade, it withdraws purchase cable from the
arresting engine. This action causes the crosshead
to move toward the fixed sheave end of the engine.
In addition to causing fluid displacement from the
engine cylinder, the movement of the crosshead
causes the CRO valve drive system (fig. 3-1) to
rotate the CRO valve cam. Rotation of this cam
forces a plunger down onto a set of levers (fig. 3-4),
which in turn forces a valve sleeve and valve stem
down to mate with a valve seat to close the valve,
shutting off the flow of fluid from the engine
cylinder to the engine accumulator, bringing the
aircraft to a stop.
As stated earlier, the CRO valve is designed to
bring all aircraft, regardless of weight, to a
controlled stop while using approximately the same
amount of flight deck landing area.
This is
accomplished by adjusting the allowable opening of
the CRO valve, a smaller, more restrictive opening
to arrest a heavy aircraft or a large valve opening to
arrest a light aircraft.
Control Valve Weight Selector
The aircraft weight selector makes it possible to
adjust the valve for aircraft of different weights by
varying the valve opening. See figure 3-4.
The size of the initial valve opening is adjusted
while the arresting engine is in the BATTERY
position. The lead screw receives rotary motion
from the motor unit or handwheel and converts it
into Iinear motion. This linear motion positions the
upper lever and drives the local and remote
indicators.
In each of the two levers (upper and lower), the
distance between the fulcrum and roller is constant.
On the upper lever, the distance between the
fulcrum and the point of application of force from
the cam is variable, its greatest length being twice
that of the lower lever. The lever arm ratio of each
lever, therefore, is variable between 1:1 and 2:1.
When the upper lever is fully extended, the ratio
of each lever is 1:1.
In this setting the initial
opening of the control valve upon engagement of an
3-6
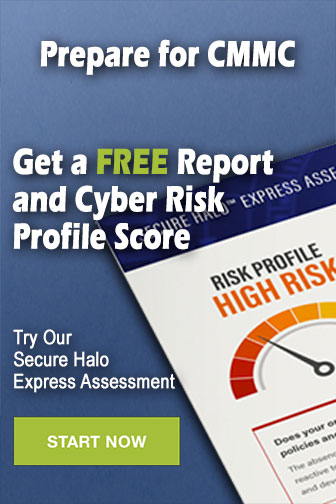