starboard. On ships equipped with deep centerlines,
double-bottoms, and peak tanks, additional lines are
required to strip these tanks.
The service-tank stripping tailpipe extends from 1
1/2 inches off the tank bottom and is connected di-
rectly to the suction header of the motor-driven strip-
ping pumps. These lines are fitted with a cutout valve,
and a one-way check valve or spectacle flange.
The pump piping is arranged to take suction from
the common suction header and discharge into the
common discharge header. The two cutout valves in
the suction header permit both pumps to take suction
from either the port or starboard tanks independently,
or from both sides simultaneously. The pump inlet
piping contains an inlet valve, a compound gage, and
on some ships, a 40-mesh basket-type strainer. The
discharge piping contains a valved sample connec-
tion, pressure gage, a discharge valve, and a one-way
check valve. From the discharge header, the stripped
liquid can be directed to the contaminated-JP-5 set-
tling tanks, or it can be directed to the transfer main
when consolidating the fuel load.
Hand-Operated Stripping
System
The hand-operated stripping system (fig. 4-4) is
provided specifically for JP-5 service tanks. Its pur-
pose is to remove water and solids from the bottom of
the tanks.
The hand-operated stripping system tailpipe ex-
tends from 3/4 inch off the service tank bottom and is
connected to a tanktop cutout valve. The lines from
each service tank in the pump room are combined and
connect directly to the suction side of the hand-oper-
ated stripping pump. The discharge line contains a
sight glass, sample connection, one-way check valve,
and discharge cutout valve. The stripping line dis-
charges into the contaminated-JP-5 settling tank or
purifier sump tank.
SERVICE SYSTEM
The service system (fig, 4-5) contains all the pip-
ing, valves, and related equipment necessary to de-
liver clean, clear, and bright JP-5 from the service
tanks on the eighth deck to aircraft on the flight and
hangar decks.
With the ability to isolate the service system into
four separate quadrants, the general arrangement of
this system is nearly identical on all earners. But the
actual piping, valves, and related equipment will defi-
nitely vary. The service system described here is the
forward section of a typical CV.
The service system piping in the pump room (fig.
4-6), begins with the service-tank suction tailpipes.
These lines extend from 24 inches off the tank bottom
to the service-pump common suction header. Each
line is fitted with a shutoff valve to isolate the tank
from the system when not in use.
The service pump common suction header is di-
vided into a port and starboard suction header by a set
of crossover valves. During normal operations, these
crossover valves are open to allow the use of any
service pump with any service tank. Additionally, the
cross-connections from the transfer pump suction
header, fitted with a spectacle flange or line blind
valve, and a cutout valve interconnect with the service
pump suction header between these valves. This ar-
rangement allows two service pumps to be used as
transfer pumps, and two for servicing aircraft. Of
course, this would bean emergency arrangement if all
three transfer pumps were disabled. Otherwise, the
cross-connection is only opened to allow service
pumps to be used for off-loading JP-5.
The service pumps are connected to the suction
header by the pump inlet. This line contains an inlet
valve and a compound gage. The discharge line, con-
necting the pumps to the common discharge header,
contains a recirculating line, pressure gage. one-way
check valve, and a discharge valve.
The recirculating line has an orifice to recirculate
about 5% of the rated capacity of the pump back to the
service tank from which suction is being taken. The
recirculated fuel through the pump casing keeps the
pump cool during standby condition. This is when the
system is pressurized (pumps are running), but no fuel
is being drawn topside. The recirculating lines (one
for each service pump), terminate in a recirculating
header. The header in turn is connected to each ser-
vice tank recirculating line. These lines, fitted with
shutoff valves, terminate 18 inches horizontally off
the tank bottom. A number of 1-inch holes, equally
spaced along the top of the recirculating line allow
JP-5 to be returned to the tank without disturbing the
contents of the tank. When the system is being set up
for operation, the recirculating header MUST be
aligned to the service tank from which suction will be
taken. Also, when the service tank is changed, so must
the recirculating header.
4-7
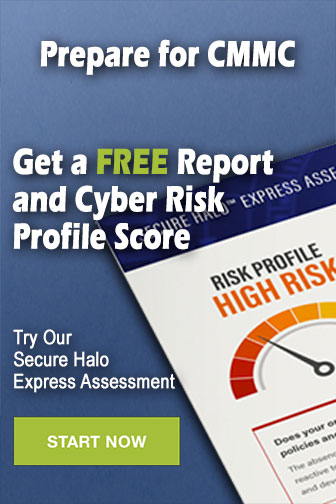