EXHAUST CONE ASSEMBLY.The exhaust
cone (fig. 6-13), attached to the rear of the turbine
assembly, is a tapered, cylinder-shaped outlet for the
gases. The cone eliminates turbulence in the emerging
jet, thereby giving maximum velocity.
The inner cone is usually attached to the outer cone
by streamlined vanes called brace assemblies. The
exhaust cone itself is usually made of stainless steel
sheets, reinforced at each end with stainless steel
flanges. As much heat energy as possible is kept within
the exhaust cone. A covering of layers of aluminum foil
or other material acts as insulation for the cone.
Turboprop Engines
There are numerous models of the turboprop
engine. The P-3 and E-2 aircraft are examples of
aircraft that use turboprop engines.
The turboprop engine was developed to provide the
power requirements for aircraft of greater size, carrying
capacity, range, and speed. The turboprop engine is
capable of developing 2 1/2 horsepower per pound of
weight.
The turboprop converts most of its gas-energy into
mechanical power to drive the compressor, accessories,
and a propeller. The additional turbine stages needed to
drive the extra load of a propeller create the
low-pressure, low-velocity gas stream. A small amount
of jet thrust is obtained from this gas stream.
The turboprop engine (fig. 6-14) consists of three
major assemblies: the power section, the torquemeter
assembly, and the reduction gear assembly. The
propeller assembly mounts on the reduction gear
assembly to provide aircraft thrust.
6-8
Figure 6-13.Typical exhaust cone assembly.
Figure 6-14.T56 turboprop engine.
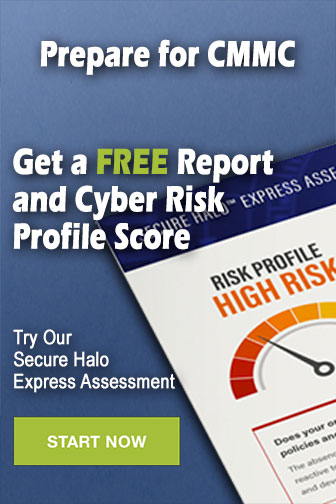