Turboshaft engines have a high power-to-weight
ratio and are widely used in helicopters. Figure 6-16
shows a typical turboshaft engine.
This engine is an axial-flow turboshaft engine
incorporating the free turbine principle. It is comprised
of a compressor, combustor, gas generator turbine, and
power turbine. The engine is equipped with a control
system that modulates fuel flow to maintain constant
power turbine output speed for a given speed selector
setting in the governed range. This system maintains
the selected speed by automatically changing the fuel
flow to increase or decrease gas generator speed. The
pilot determines the speed by positioning the power
lever. The control system provides automatic protec-
tion against compressor stall, turbine overtemperature,
overspeed of either turbine assembly, and combustion
flameout.
An emergency throttle system is provided for use in
case of fuel control failure. A starter, mounted at the
nose of the engine, drives the gas generator rotor and
engine accessories for engine starting. The engine is
installed with its nose facing forward and supported by
engine mounts bolted to the aircraft fuselage. Air is
supplied to the engine through the inlet air duct, located
inside the right-hand side door of the center nacelle. An
alternate air door is attached to the duct by a hinge. Air
is supplied through the alternate air door when an
insufficient amount of air comes into the engine
through the main air duct. The engine is installed so that
with
the
nacelle
removed,
all
accessories
and
components can be easily reached and maintained.
Turbofan Engines
There are also many different models of this type of
engine. The S-3, AV-8, and F/A-18 are examples of
aircraft that use this engine.
The turbofan engine (fig. 6-17) is similar to the
turboprop, except a fan replaces the turboprop
propeller. One basic operational difference between the
two engines is the airflow. The fan is inside a cowling,
and as a result the airflow through the fan is unaffected
by the aircraft's speed. These factors eliminate loss of
operational efficiency at high speeds, which limits the
maximum airspeed of propeller-driven (turboprop)
aircraft.
The turbofan engine has a duct-enclosed fan
mounted at the front or rear of the engine. The fan runs
at the same speed as the compressor, or it may be
mechanically geared down. An independent turbine
located to the rear of the compressor drive turbine may
also drive the fan.
The fan draws in more air than the compressor of a
turbojet engine because of the larger area of the inlet.
Because the larger amount of air is compressed and
accelerated by the fan, the air completely bypasses the
burner and turbine sections of the engine and exits
through the fan exit ducts. Since the air is not heated by
burning fuel to obtain thrust, the turbofan engine has
lower fuel consumption. To develop thrust, the turbofan
engine accelerates a large amount of air at a relatively
low velocity, which improves its propulsion efficiency.
Compared to the turbojet, the turbofan engine has a
low engine noise level. The low noise level results from
the lower gas velocity as it exits the engine tailpipe.
One reason for the decreased velocity is an additional
turbine stage in the engine. This additional turbine
stage extracts power from the exhaust gases to drive the
fan.
The aircraft powered by a turbofan engine has a
shorter takeoff distance and produces more thrust
during climb than a turbojet of approximately the same
size. This extra thrust allows the turbofan aircraft to
take off at a much higher gross weight.
Gas Turbine Engine Component Controls,
Systems, And Sections
In addition to the five major components discussed
as part of the turbojet engine, there are numerous
controls, systems, and sections that are common to all
four types of gas turbine engines. Among the more
important of these are the fuel control, lubrication
system, ignition system, and accessory section.
FUEL CONTROL.Depending upon the type of
engine and the performance expected of it, fuel controls
may vary in complexity. They may range from simple
valves to automatic computing controls containing
hundreds of intricate, highly machined parts.
The pilot of a gas turbine powered aircraft does not
directly control the engine. The pilot's relation to the
power plant corresponds to that of the bridge officer on
a ship. The bridge officer obtains engine response by
relaying orders to an engineer below deck, who, in turn,
actually moves the throttle of the engine.
Modern fuel controls are divided into two basic
groups, hydromechanical and electronic. The controls
sense some or all of the following engine operating
variables:
1.
Pilot's demands (throttle position)
6-11
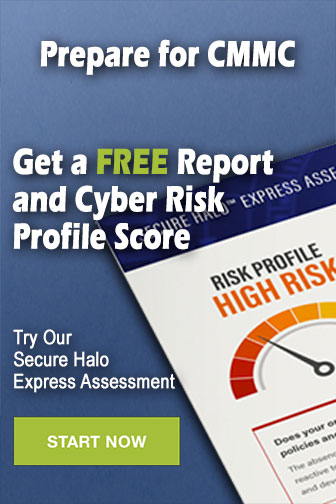