The supporting documentation may vary by
circumstances but should consist of the following
documents:
1. For adjustments or reversals requiring
preliminary research, a checklist of actions taken during
preliminary research such as search of adjacent
locations, research of unposted or erroneous
transactions, or verification of catalog data.
2. For adjustments or reversals requiring causative
research, the following is a list of the necessary
supporting documentation:
l
l
l
l
l
l
l
l
l
A checklist of actions taken during preliminary
research
Receipt, issue, or transfer documents relating to
the investigation
Cumulative transaction ledger or master stock
record probes
Survey documents
Unmatched listings
Repair parts petty officer (RPPO) or AIMD logs
Mandatory turn-in repairable (MTR) or carcass
tracking documents (including beyond
capability maintenance [BCM] log)
Detailed list of DLRs
Any other supporting documentation
Inventory Count Procedures
A complete and correct item count is basic to a
physical inventory which, in turn, results in greater
stock record accuracy and better inventory control.
Detailed procedures for the inventory count afloat are
described in Automated SNAP 1 Supply Procedures,
NAVSUP P-567, and Afloat Supply Procedures,
NAVSUP P-485.
The inventory options available for use on
SUADPS-RT ships readily adapt to the inventory
schedule and needs of the inventory supervisor. In
automated ships, the inventory supervisor can tailor the
inventory in anyway that fits the applicable needs. You
should familiarize yourself with all the applicable
document identifiers to perform a specific task.
Recording Inventory Results
on
The results of physical inventory must be recorded
the manual or automated files used by the activity.
For manual procedures, refer to NAVSUP P-485. For
automated procedures, refer to SUADPS-RT support
procedures or other supporting publications.
Inventory Accuracy Standards
Upon completion of the physical inventory and
reconciliation of the stock records, the count and
adjustment documents must be reviewed. The
documents are reviewed to determine the number of
items inventoried and the number of location or
quantity errors both corrected or adjusted. As a
minimum, an accuracy rate of 90 percent is considered
acceptable (refer to TYCOM instructions for additional
guidance on validity standards). If the accuracy rate is
below standard, the supply officer immediately initiates
action to ensure more effective maintenance of stock
records.
Location Audits
The purpose of the location audit is to verify that
material in storage locations agree with the location in
the stock record. A location audit should be scheduled
so that it is done just before the scheduled inventory of
a particular storage area. All storage areas (100
percent) must be audited on an annual basis.
A well-managed location audit program (LAP)
reduces inventory efforts and improves the supply
effectiveness and inventory accuracy. The LAP also
improves the use of all available storage space.
PROCEDURES. Location audit procedures are
contained in NAVSUP Instruction 4440.185,
TYCOMs directives, and NAVSUP P-567. The stock
number, location, unit of issue, and shelf-life expiration
date are verified during a location audit.
LOCATION AUDIT VALIDITY. The location
validity rate is computed upon completion of a location
audit for a particular storeroom or storage area. The
accuracy rate for a location audit is 98 percent. The rate
is computed by auditing 5 percent of the locations
involved and subtracting the number of erroneous
locations from the total number of locations audited.
Then, divide the difference by the total number of
locations audited and the result is the accuracy rate. As
an example, for 850 locations validated with 17 errors,
the following applies:
850-17=833
833 + 850= 98% accuracy rate
An accuracy rate of less than 98 percent for a
particular storage area is considered unsatisfactory and
5-18
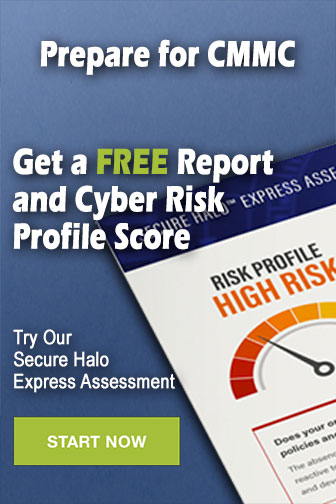