l Maintaining adequate accountability of
material and equipment on custody.
. Maintaining inventory control of autho-
rized allowances of material listed in the individual
material readiness list (IMRL).
. Validating not mission capable supply/
partial mission capable supply (NMCS/PMCS)
requisitions daily and maintaining (by aircraft
bureau number) current NMCS/PMCS status
records.
l Performing an inventory of aircraft, with
technical assistance, upon receipt or transfer, and
making sure inventory log entries are made and
inventory shortage listings are prepared and
forwarded to maintenance control for inclusion
in the aircraft inventory record (AIR).
. Maintaining control and records to
guarantee turn-in of defective components within
established time frames.
ORDERING PARTS AND MATERIAL
Rapid communication between the material
control code (MCC) and the SSC is effected
through the use of data transmission equipment.
The effective use of communication devices
permits maximum coordination between supply
and maintenance, thereby improving the overall
material management program. Communication
equipment may include telephones, radios,
teletypewriters, and computers. When material or
parts are ordered, material control should take
action as follows:
l Receive requirements from work centers,
support areas, and so forth.
l Forward requirements to the SSC using
locally approved methods of communication.
Make sure the data provided to the SSC is clear
and legible and that a document number is
assigned.
l Enter the date and time that the material
was ordered in the material control register to
reflect the exact time of submission to the SSC.
This time is required for determining accurate
NMCS/PMCS start time and conducting follow-
up inquiries.
l When a repairable component is ordered,
make sure the defective component is available
for simultaneous exchange.
In some instances, it is not feasible or
advisable to remove a repairable component until
a replacement is in hand. The items in this
category are identified in the Consolidated
Remain-in-Place List (CRIPL). The respon-
sibilities and procedures for establishing, main-
taining, and modifying the CRIPL are in
OPNAVINST 4420.25. Items identified in the
CRIPL are the only authorized exceptions to the
one-for-one exchange rule.
RECEIPT OR DELIVERY OF
PARTS AND MATERIAL
Upon receipt of material or parts, material
control has the following responsibilities:
. Receives the material and DD Form 1348
(or facsimile form) from the SSC material delivery
unit.
l Signs the DD Form 1348 hardback copy
as a receipt (yellow, green, and hardback for
repairable).
. Enters the date and time the material is
delivered to the specified delivery point on the DD
Form 1348 pink and hardback copies and in the
material control register or request document
facsimile. This time is required for determining
accurate NMCS stop time.
l Distributes received parts and material to
the appropriate work center or work area.
. Obtains the signature of the work center
personnel receiving the material on the DD Form
1348 pink copy and files the copy in the completed
requisition file.
. Turns in defective repairable CRIPL
components within 24 hours.
UNSATISFACTORY ISSUES
Instances will occur when the supply response
section (SRS) delivers material that does not
5-2
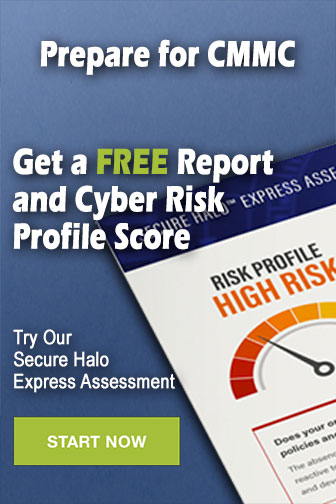