In block GG, enter the name and rank or grade of
the person approving the transfer. The approving
individual signs above the printed name in this block.
DISTRIBUTION OF DOCUMENTS
Distribute copies of DD Form 1348-1 as follows:
Copy 1 (original) is the activity copy. The activity
retains copy in the expenditure invoice file as proof
of shipment or turn-in.
Copies 2 and 3 are the consignee copies. Place these
copies inside the container with the material.
Copy 4 is also the consignee copy. For unclassified
material copy 4 in a waterproof envelope and
attach it to the No. 1 shipping container. For classified
material, place copy 4 with copies 2 and 3 inside the
container with the material.
Copy 5 is the miscellaneous copy. An activity may
retain this copy for local use, or otherwise discard it.
Also, an activity may forward this copy to higher
authority when turning in specific items. See NAVSUP
P-485, chapter 5, paragraph 5068, for more details.
Copy 6 is the suspense copy (when needed), which
is used expenditure invoice file until receipt of a
signed copy 1.
When procedures require proof of receipt, get
signature on copy 1 of the DD Form 1348-1. Turn-in of
the following classes of material requires receipt
signature:
Classified
Controlled equipage
Controlled reactor plant parts
Mandatory turn-in repairable or AVDLR
Sensitive or pilferable items
Small arms, ammunition, and explosives
When shipping these items, you should not open an
original container for the sole purpose of putting the
consignee copies inside. In this case, put copies 2 and 3
with copy 4 in a waterproof envelope. Then, attach the
envelope, with documents, to the No. 1 container.
PREPARATION OF MATERIAL
FOR TURN-IN
Before offloading, you must ensure materials have
proper identification, tags, and markings. This will help
the receiving activity process and report the receipt of
material. The following rules will help you prepare
material correctly.
. Distribute copies of DD Form 1348 as described
in previous paragraphs. When shipping more than one
piece of material on a single document, attach the
document on the No. 1 container.
. Mark radioactive materials with proper labels
and separate them from other materials.
. Process unserviceable AVDLR items according
to OPNAVINST 4790.2 (series), NAVSUP P-545, and
the Master Repairable Item List (MRIL). Provide
protection to the material according to NAVSUP P-484
and section C0030 (Packaging Data for ASO and
NAVAIR Repairables).
. Separate ready-for-issue non-NSN items.
l Separate materials destined for turn-
DRMO.
. Separate heavy items from delicate or small
items.
. Separate materials with an extended line item
value of or less to ease handling by the receiving
activity.
. Mark containers, with only one item inside, with
the stock number of the item.
. Remove flares and narcotics from life rafts prior
to turn-in.
l Remove batteries from equipments before
turn-in.
OFFLOAD PROCESSING
Automated ships perform offload processing partly
by computer and manually by stock control and storage
personnel. The offload process includes selecting
material candidates and preparing documentation.
Storage personnel use the document to locate, pick,
stage the material, and send a copy back to stock control.
Stock control uses the document to update and process
offload records. Shipping personnel check the
documents and material and deliver/ship the material.
During storage process, personnel use the DD Form
1348-1 to locate, count, and stage excess material.
During this phase, personnel may make changes to the
OFFLOAD and RETAIN QUANTITY on the
document.
7-21
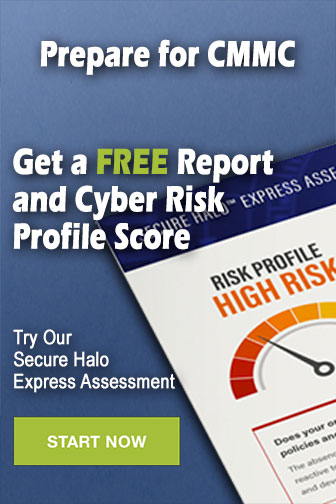