maintenance officer or supervisor can carry out their
duties more effectively and efficiently. Set up the
material control VIDS according to OPNAVINST
4790.2 (series). After receiving a material request from
a work center, transmit the demand to the supporting
supply activity. Use the requisition priority and project
code assigned by production control. Advise
maintenance or production control and the work center
of the document number assigned. Place a copy of the
facsimile transceiver form, register, or other form on the
VIDS board. You may use color tabs on the request form
to indicate the priority or project code used.
NOTE: Activities using the Naval Aviation
Logistics Command Management Information System
(NALCOMIS) should refer to the users manual. Some
activities that use NALCOMIS do not use VIDS to
maintain files.
Hardware
VIDS display boards consist of enlarged
cardex-type pockets for the visual display of weapons
systems or component status. Each pocket overlaps the
one below it, with an approximately 3/8-inch strip
visible at the bottom pocket. VIDS boards are available
in 100, 50, and 25 pockets.
Material Requisition Register
MCC use the Material Requisition Register
(OPNAV 4790/11) to transmit demands to ASD when
other means is not available. MCC uses this form to
display AWP status. Data sequence is compatible with
key entry and the MILSTRIP.
Software
Items used for the operation of the VIDS may be
obtained from the supply system or commercial
vendors. These items include signal tabs, file containers,
replacement pockets, and three-ring binders.
AIRCRAFT INVENTORY RECORDS
Activities with assigned aircraft or that maintain
aircraft must be familiar with the aircraft inventory
record (AIR). The purpose of the AIR is to provide a
continuous chain of accountability for specific
equipment and material. The equipment or material may
be installed on or designated for use on any aircraft of a
specified type/model/series. The following text lists the
items that make up the AIR. Refer to OPNAVINST
4790.2 (series) for detailed description of each part.
. Binder (OPNAV 4790/109).
. Title Page and Sectional Breakdown Diagram
(OPNAV 4790/110).
l Equipment List (OPNAV 4790/111).
. Shortages (OPNAV 4790/112).
. Certification and Record of Transfer (OPNAV
4790/104)
Master Aircraft Inventory Record
The Commander, Naval Air Systems Command
(NAVAIR) maintains the Master Aircraft Inventory
Record (MAIR). The MAIR identifies those items of
installed and loose equipment that require a periodic
inventory. A MAIR shall be maintained as the standard
for each type/model/series aircraft. The MAIR serves as
a checklist for items requiring an inventory. Also, it
provides reasons/authority for any shortages that exist
and documents certificates of accountability.
Equipment Accountability
In addition to the accountability of AIR items, an
accounting of equipment will be done prior to aircraft
transfer. These are equipments listed in or comprising
subsystems of the applicable mission essential
subsystem matrix (MESM). A number of MESM items
are identified at the subsystem level rather than by exact
equipment designation. Therefore, you cannot use the
MESM totally as a specific equipment checklist as you
can the AIR. The accounting of most MESM items is by
system operation checks and maintaining a VIDS/MAF
file vice an AIR-type accountability. When transferring
aircraft equipment accountability, those missing
MESM-related items will be identified in the AIR as
shortages, even though that specific equipment is not
listed.
Aircraft are transferred and accepted only after
completion of equipment/item inventory and notation
on the forms of the AIR. In most instances of aircraft
transfer, the inventory is accomplished based on the
selected equipment and material listed in the AIR and
systems identified in the MESM. The following
paragraphs provide a list governing the selection of
items to be included in the AIR. These items may be
government-furnished equipment (GFE) or
contractor-furnished equipment (CFE).
8-16
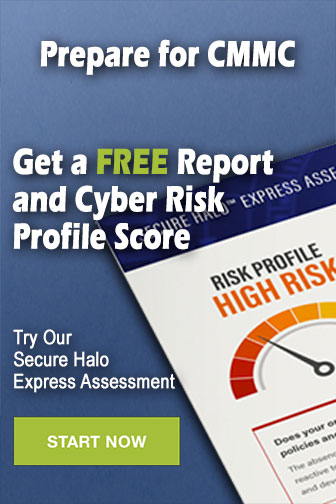