CHAPTER 8
MATERIAL CONTROL
The Naval Aviation Maintenance Program (NAMP)
describes policies, procedures, and responsibilities at All
levels of aviation maintenance. It is the basic document
and authority governing the management of all aviation
maintenance. It is sponsored and directed by the Chief
of Naval operations (CNO).
The NAMP provides an integrated system for
performing equipment maintenance and all related
support functions. The support functions described in
the NAMP include material control. On 26 October
1959, the CNO established the NAMP, and the Chief of
the Bureau Of Aeronautics implemented it. On 1
January 1965, the Navy Maintenance and Material
Management (3M) System was introduced. This system
is what we know now as AV-3M. The 3M System
provided maintenance data collection and man-hour and
aircraft accounting systems as part of the NAMP. In
January 1968, the VNO noted that the major
implementing directives of the NAMP needed revision
to ensure a cohesive and command-oriented
publication. The directives were consolidated into a
single family of documents. The result was
OPNAVINST 4790.2, issued in July of 1970. Several
revisions of the OPNAVINST 4790.2 followed to
continually upgrade readiness and safety standards
established by the CNO.
The contents of the NAMP provides information for
all parts of aviation maintenance. It describes what to
do, when to do it, where it will be done, and who is to
do it. All aviation activities base their policies, plans,
programs, and procedures on the NAMP. Whenever the
Navy accepts a new model aircraft, it is expected that
these aircraft fill a specific need for a given length of
time. The purpose and mission of the aircraft are the
basis for planning the requirements to support them.
These include personnel, facilities, and material
requirements. For this reason, all personnel associated
with naval aircraft need to become familiar with the
NAMP.
The Naval Aviation Logistics Command
Management Information System (NALCOMIS) is an
integrated, on-line, real-time system. NALCOMIS is
designed to collect, store, process, and distribute data
according to NAMP procedures by using a computer
system. The computer terminals, magnetic tape drives,
and communications net work arc the devices used to
enter data in NALCOMIS. The terminals are the
primary input devices because of the on-line and
interactive nature of thes system. Terminals are available
for data input by system users with proper access
authorization. A valid password is required as an input
to sign on to NALCOMIS. An authorized user will be
able to sign on from any terminal within the
NALCOMIS environment. NALCOMIS will process
the passwords in such a way that it recognizes the user
signing on and the users assigned organization, work
center, and special maintenance qualification (SMQ). A
user will be assigned only one password. The SMQ
assigned to each person determines his/her ability to
access a specific NALCOMIS conversation. Once a
user is allowed access to a conversation, the users SMQ
and detailed maintenance qualifications will control
data modifications at the data element level in
NALCOMIS. After signing on to NALCOMIS, the user
will be allowed to access most of the data base by
selecting an inquiry option on a menu and providing any
necessary key prompt information.
NALCOMIS can provide data either by screen
display, a hardcopy report, or external interface record.
The information displayed on a screen in response to a
users input will be provided only if the user has the
necessary SMQ to perform the transaction. Only
authorized users will be allowed to request a report to
be printed. The external interface records are
automatically generated upon successful completion of
the related transaction.
Potential users should attend the appropriate
training class(es) prior to receiving access to
NALCOMIS.
This chapter describes the procedures according to
OPNAVINST 4790.2 (series). It also contains basic
information about the NALCOMIS.
Aviation Storekeepers are responsible for providing
parts, equipments, and materials needed by
maintenance. The AK accomplishes this through the
material control of a squadron or intermediate
maintenance activity (IMA). The AIRMAN training
manual describes the organization of the aircraft
8-1
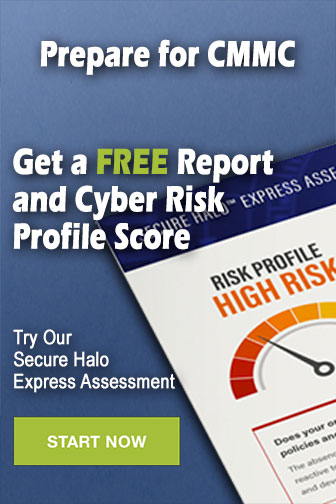