one valve, and the other is powered by the utility
hydraulic system.
The power cylinder is a single tandem cylinder,
composed of four chambers with pistons connected to
a common shaft. Each of the two control valves
operates on that portion of the power cylinder to
which it is associated.
Both hydraulic systems
operate simultaneously, and each delivers 3,000-psi
pressure to the mechanism. If one hydraulic system
should fail, the other system will supply enough
power to operate the ailerons at reduced hinge
movement.
When the control stick moves, the control cables
move the power mechanism sector. Through linkage,
the sector operates the control valves, which direct
hydraulic fluid to the power cylinder. The cylinder
actuating shaft, which is connected to the power crank
through a latch mechanism, operates the power crank.
The crank moves the push-pull tubes, which actuate
the ailerons. In the event of complete hydraulic
power failure, a handle in the cockpit maybe pulled to
disconnect the latch mechanisms from the cylinder.
When the handle is pulled, it places this particular
aileron system in complete manual operation. In
manual operation, the power cylinder is disconnected
from the cable sector, causing the control stick to
manually move the ailerons at a reduced rate.
The lateral control system incorporates a
load-feel bungee, which serves a dual purpose. See
figure 9-9. The bungee provides an artificial feel and
centering device for the aileron system.
It is
interconnected between the aileron system and the
aileron trim system.
Energizing the aileron trim
actuator moves the bungee operating the power
mechanism, which repositions the aileron control
system to a new neutral position.
In normal operation of the control system, when
the control stick is actuated left or right, the power
mechanism compresses the bungee. The compressed
bungee returns the stick to the neutral position upon
release of the stick.
Figure 9-9.Aileron power mechanism.
9-11
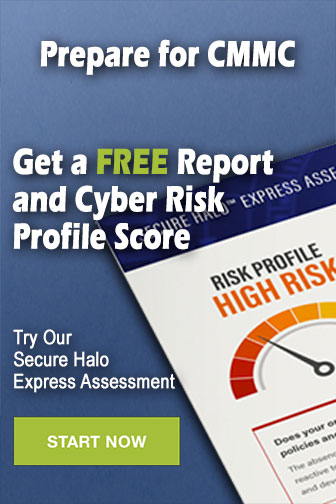