threaded power screw.
The actuator is manually
controlled through inputs from the trim switch on the
control stick grip. When the stabilizer is in automatic
trim, the actuator receives inputs from the AFCS.
High speed is used during manual trim, and low speed
during automatic trim.
The stabilizer shifting mechanism, shown in
figure 9-7, consists of a shift sector and its linkage,
plus cable that runs from the flap drive gearbox and
the rudder cam shift mechanism. A spin recovery
cylinder is also attached to the shifting mechanism,
and provides an alternate method of shifting the
stabilizer and rudder from the clean configu-
ration to the dirty, or increased throw con-
figuration.
In normal operation, when flaps are extended, a
cable running from a drum on top of the flap drive
gearbox to the sector assembly of the shifting
mechanism rotates the sector. Linkage connecting the
sector assembly and the control stick linkage is
shifted. Linkage shifting increases control stick
travel. Stabilizer down travel is increased to a
24-degree maximum. A cable is also connected from
the sector assembly to the rudder cam stop shifting
mechanism, which increases rudder travel from 4 to
35 degrees each side of neutral.
The pilot, at his/her option, may obtain increased
stabilizer and rudder throw by actuation of the spin
recovery assist switch, eliminating the necessity of
lowering the flaps.
This action ports hydraulic
pressure through the spin recovery selector valve and
its flow regulators and check valve to the spin
recovery cylinder, causing it to extend and shift the
mechanism in the same manner as provided by the
cable action.
The two nonbypass-type filters in the system
protect the intricate valving mechanisms of the
actuator from contamination, and are vitally
important to proper stabilizer operation. They are
checked with the requirements listed in the
maintenance requirements card deck, and should not
be overlooked when troubleshooting stabilizer system
malfunctions.
The stabilizer power package, used on various
Navy aircraft, is linked to the approach power
compensator system (APC). This system aids the
pilot in maintaining optimum angle of attack for
approach and landing.
An APC potentiometer is
mechanically linked to the power package, and
provides electrical inputs to the APC system to
compensate for changes in pitch attitude required
during landing approaches. The APC system
regulates the throttle position to provide the
engine thrust required to establish and maintain
the desired angle of attack. The potentiometer
provides inputs relative to the position of the
horizontal stabilizer.
Horizontal Stabilizer Control System
(Double Axis)
Because of the complexity and interrelationships
of the flight control systems of newer model aircraft,
only a brief description of a representative stabilizer
control (pitch/roll. axis) follows. This system allows
pitch about the aircrafts lateral axis and roll about the
aircrafts longitudinal axis.
Stabilizer control, which affects both the pitch
and roll axis, is provided by forward or aft and/or
left or right movement of the control stick grip.
Forward or aft movement provides pitch-axis
control; left or right movement, roll-axis control.
The control, stick grip movement is mechanically
transferred to the left and right stabilizer servo
cylinders through the pitch and roll command
summing network, the feel assemblies, and the
summing network.
These servo cylinders, which
are normally powered by the flight and combined
hydraulic power systems, move the stabilizers. If
both hydraulic systems fail, the stabilizer servo
cylinders automatically receive hydraulic power
from the backup system. The trim switch on the
control stick grip enables trimming of the aircraft in
pitch and roll.
LATERAL CONTROL SYSTEMS
Lateral control systems control roll about the
longitudinal axis of the aircraft. In this section,
several of the different system arrangements used by
aircraft manufacturers are described, and general
maintenance requirements
systems are discussed.
for primary flight control
9-9
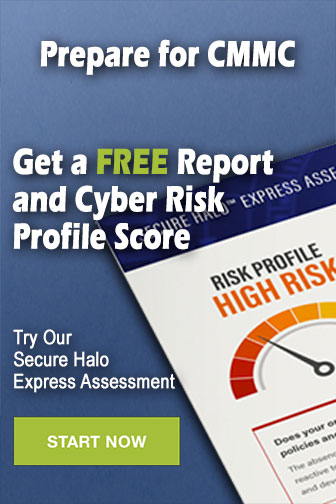