can be misinterpreted, and the resultant write-up in
the aircraft discrepancy portion of the aircraft flight
record book may be vague or misleading. To gain
further insight regarding the vague discrepancy, the
maintenance crew should question the pilot who
experienced the malfunction.
Isolating the mechanical and hydraulic portion of
the flight control system from systems that provide
automatic input will serve to pinpoint the actual
problem area. The MIM provides troubleshooting/
trouble analysis aids and appropriate schematics. The
MIM allows for the systematic checking out of the
system and associated components. In some MIMs
these aids are general in nature and limited to the
more common causes of failure. Several MIMs
combine the operational checkout procedures with
trouble analysis aids.
Steps of the checkout
procedures are performed in rigid sequence, and any
discrepancy must be corrected before proceeding to
the next step.
A thorough knowledge of the system involved
and consistent use of the mechanical and hydraulic
schematics will expedite the trouble analysis process.
Excessive time required for troubleshooting should be
documented on a separate VIDS/MAF. This will
separate the actual repair time from troubleshooting
time. Separate VIDS/MAFs provide more accurate
input information to the Maintenance Data Reporting
System.
When the malfunction has been determined and
corrected, the complete system should be opera-
tionally tested. Testing should occur in all modes of
operation to verify system integrity. Quality
assurance inspection during repair progression,
testing, and of the end product is a must. When
prescribed in the applicable periodic maintenance
information cards, test flight requirements are
mandatory. The test flight pilot is briefed by a
qualified quality assurance representative regarding
the nature of the discrepancy and corrective action
taken.
ALIGNMENT AND OPERATIONAL
CHECKS
Procedures for rigging flight control systems vary
with each type of aircraft. Applicable MIMs provide
a list of tools, special equipment, preparatory con-
siderations, and step-by-step instructions for rigging
systems.
On some aircraft, the system rigging divides into
a series of sections, such as the control stick, control
mechanism, power control actuator, and cables. If
only that section of the system has been affected, it
may not be necessary to rig the complete system.
Pushrods, bell cranks, and idlers are installed so
that end play is eliminated. They should be free to
rotate without binding. Cables should be inspected
for corrosion, broken strands, and proper tension.
Correct cable tension is necessary to obtain proper
response of the control surface. Low cable tension
may cause sluggishness, free play, and flutter of the
control surface. Excessively high cable tension will
cause increased system friction and may result in
damage to pulleys, bell cranks, or the cable itself.
A variety of fixtures, pins, and blocks are
available for performing alignment and rigging
checks on flight control systems. Neutralizing
(locking the controls and linkage in a predetermined
position), as described in the aircraft MIM, is required
during the alignment and adjustment of the flight
controls.
NOTE: Installation and removal of the
fixtures, pins, and blocks should not require
excessive force.
Slight pressure is per-
missible because of the system tolerance and
temperature effects on the aircraft. Always
refer to the MIM for tolerance information.
Figure 9-18 shows the throw board used to check
the travel of a horizontal stabilizer. The throwboard is
held in place by two wingnut attachment screws.
Before tightening these screws, the throwboard is
positioned so that the alignment hole at the
zero-degree mark is in line with the alignment screw
in the aircraft fuselage.
Control surface throws may be measured in
degrees and minutes or inches and fractions.
Figure 9-19 provides an example of an aileron throw
indication in degrees (0) and minutes (). The
protractor scale is calibrated in 30-minute increments.
The indicator reads 3 degrees 40 minutes obtained as
follows:
1. Read 3 degrees 30 minutes, as shown on the
protractor scale.
2. Since the indication mark does not fall directly
on the calibrated mark of the protractor scale, look for
the closest alignment of indicator and protractor
calibrated marks in the direction of indicator travel.
9-24
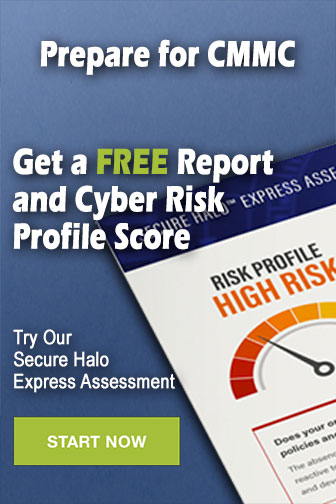