hydraulic system pressure line switches control the
operation of this system.
The two switches in the pressure lines to the
backup flight system are wired normally closed at
zero pressure. The backup pump outlet pressure
switch is wired to normally open at zero pressure.
The switches actuate at 900-1,100 psi on rising
pressure and 700-900 psi on decreasing pressure.
Closing of the combined or flight system pressure
switches energizes the backup system motor pump.
Closing the outlet pressure switch lights the backup
hydraulic system indicator light on the annunciator
panel in the cockpit.
When pressure in the flight and/or combined
hydraulic system decreases to 700-900 psi, the system
is automatically activated. The system isolates a
portion of the combined system in the tail of the
aircraft by check valves in the pressure lines and a
shutoff valve in the return line. When the shutoff
valve closes, it stores a full charge of fluid in the
backup system reservoir,
The reservoir mounts on top of the motor-pump
assembly. It has a capacity of 0.84 quarts. The return
system shutoff valve is an integral part of the
reservoir end flange inside the reservoir pressurizing
spring. The soft-seated, poppet-type shutoff valve is
held open when the reservoir is at the full position.
When pressure drops and the reservoir piston moves
about three-sixteenths of an inch away from the full
position, the spring-loaded valve closes and prevents
flow from the reservoir. The shutoff valve also acts
independently as a relief valve to relieve reservoir
pressure above 95 psi.
Return fluid flow from the rudder and stabilizer
actuators fills the backup system reservoir. When the
reservoir approaches the full position, it mechanically
opens a shutoff valve, allowing return flow to go to
the combined system reservoir. In normal flight, the
40-psi return system pressure is enough to maintain
the backup reservoir piston at the full position. The
shutoff valve fully opens against its spring pressure.
If return system pressure drops below the
reservoir pressurizing spring pressure of 15 psi, the
reservoir piston moves and displaces fluid through the
shutoff valve. As the piston moves, the shutoff valve
closes fully in three-sixteenths of an inch of piston
movement.
The shutoff valve may open momentarily during
backup system operation to discharge excess fluid
volume. This action may be a result of unequal
stabilizer in-and-out stroke volume or thermal
expansion of the fluid. The shutoff valve also opens
when the flow rate exceeds the flow capacity of the
backup pump. The latter condition could occur when
the flight system is operating normally and high rate
inputs are applied to the actuators.
Pressure line isolation is accomplished by the use
of check valves. To prevent backup system leakage to
a failed combined system, a soft-seat check valve is
installed upstream of the standard metal-seat check
valve. These valves are found in the combined
system pressure line.
A three-position backup system hydraulic test
switch is located in the cockpit. The central
spring-loaded OFF position provides automatic
function in flight.
The momentary hold positions,
COMBINED and FLIGHT, are for a ground test of the
system when the aircraft is on external electrical
power. Selection of either position will energize the
motor pump when aircraft pressure is less than
700-900 psi.
A cartridge-type filter element housed within the
reservoir head and a pressure line filter protects the
system from contamination. Since the backup motor
pump is energized when either or both primary
systems fail, the following three operational
conditions can exist:
1. With the backup and flight systems operating,
normal flight control is available. The backup system
performs as an isolated system with the return shutoff
valve closed.
The variable displacement backup
motor pump has a maximum rated output of 3 gpm at
1,000-psi output pressure to zero gpm at cutoff
pressure (3,000-3,200 psi). The pump cannot match
the high rate capacity of the flight system. Backup
motor pump pressure will drop to zero when demand
exceeds 3 gpm.
Zero pressure causes the cockpit
indicator light to go out. When pressure increases to
900-1,000 psi, the light will come on again, indicating
backup system operation.
2. With the backup system and combined system
operating, normal flight control is available. The
backup system is not isolated, as normal combined
system pressure exists within pressure and return
lines.
The return shutoff valve remains open.
Combined system pumps maintain high pressure at
the rudder and stabilizer actuators. Flow demand on
the backup pump is not excessive at high rates. The
cockpit indicator light should remain on, indicating
backup system operation.
9-22
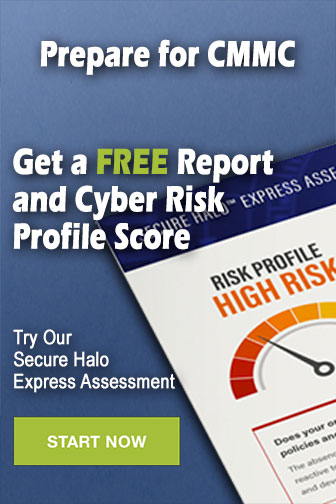