Spoiler Control System
On one model aircraft, spoiler action is provided
through the control stick grip, roll command
transducer, roll computer, pitch computer, and eight
spoiler actuators (one per spoiler). When used to
increase the effect of roll-axis control, the spoilers can
only be controlled when the wings are swept forward
at 57 degrees.
Right or left movement of the control stick grip
mechanically transfers to the roll command
transducer. The transducer converts the movement to
inboard and outboard spoiler roll commands.
Because the spoilers are vital for landing, the left- and
right-wing inboard and No. 1 mid-spoilers are
controlled by the roll computer. The spoilers are
powered by the combined hydraulic power systems.
The left and right outboard and No. 2 mid-spoilers are
controlled by the pitch computer. These spoilers are
powered by the mid-outboard spoiler/high lift backup
module. This combination provides positive spoiler
control if either computer or hydraulic power source
malfunctions.
DIRECTIONAL CONTROL SYSTEMS
Directional control systems provide a means of
controlling and/or stabilizing the aircraft about its
vertical axis. Most Navy aircraft use conventional-
type rudder control systems for this purpose.
The rudder control system, shown in figure 9-15,
is operated by the rudder pedals in the cockpit. The
system is powered hydraulically through the rudder
actuator. In the event of hydraulic power failure, the
hydraulic portion of the power system is bypassed.
The system is then powered mechanically through
control cables and linkage. An aerodynamic
irreversible hydraulic system is employed in the
rudder system.
To accomplish trim, the complete
rudder surface is repositioned.
The actuation of the rudder pedals causes the
control cables to move a cable sector assembly. The
cable sector, through a push-pull tube and linkage,
actuates the power mechanism. The rudder actuator
deflects the rudder to the left or to the right.
A load-feel bungee is connected to the push-pull
tube, and is compressed when the push-pull tube is
actuated.
When the pedals are released, the
compressed bungee returns the system to the neutral
position. In the event of hydraulic failure, a slip link
allows movement of the control valve linkage to port
hydraulic fluid from the actuating cylinder. Then the
cylinder can be mechanically driven by pilot input
during manual operation. In manual operation,
surface travels are reduced by the lost-motion effect
of the slip link.
The load-feel bungee is also the connecting link
from the rudder trim actuator to the power
mechanism. When the trim actuator is operated, the
bungee repositions the power mechanism. The power
mechanisms deflect the rudder for nose-left and
nose-right trim. Figure 9-15 is a functional schematic
of the operation of the rudder control system.
The rudder power mechanism is actuated when
movement from the cable sector assembly is
transmitted through the push-pull tube to the primary
control crank. The crank is connected to the load-feel
bungee, a slip link to the secondary crank, a link and
spring to the pedal position transmitter, and a link to
the control valve of the actuator assembly. The
actuator assembly consists of an electromechanical
dual input control valve, a rudder surface position
transmitter, and a power cylinder. When the
mechanism linkage is actuated, the control valve
directs hydraulic pressure from both the utility
hydraulic system and the surface control hydraulic
system to the power cylinder. The valve directs the
hydraulic pressure to two separate chambers in the
cylinder. Each chamber has a separate piston that is
mounted on as common shaft. The shaft is connected
to a push-pull tube that moves the rudder. The
actuator assembly normally operates from both
hydraulic systems.
If one system should fail, the
other supplies sufficient pressure to operate the
rudder with some lost hinge movement. In the event
both hydraulic systems fail, the slip link will allow
movement of the control valve linkage to port
hydraulic fluid from the actuating cylinder.
When the automatic flight control system is
engaged, the actuator initiates the movement of the
rudder system through the electrical impulse received
by the control valve from the surface control
amplifier. The pedal position transmitter and the
rudder surface transmitter function only when the
automatic flight control system is engaged.
Rudder pedal movement transfers mechanically
to the left and right rudder servo cylinders through the
rudder feel assembly, the yaw summing network, and
the reversing network. These servo cylinders,
normally powered by the flight and combined
hydraulic power systems, move the rudders. If both
9-18
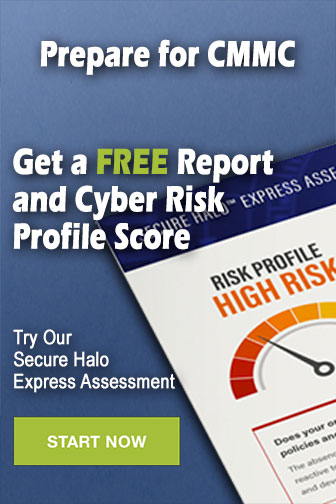