The power pump may be one used with a separate
pressure regulator control. The power pump may be
used with an integral pressure control valve that
eliminates the need for a pressure regulator. This
system differs from the open center system in that the
selector or directional control valves are arranged in
parallel and not in series. The means of controlling
pump pressure will vary in the closed center system.
If a constant delivery pump is used, the system
pressure will be regulated by a pressure regulator. A
relief valve acts as a backup safety device in case the
regulator fails.
If a variable displacement pump is
used, system pressure is controlled by the pumps
integral pressure mechanism compensator.
The
compensator automatically varies the volume output.
When pressure approaches normal system pressure,
the compensator begins to reduce the flow output of
the pump. The pump is fully compensated (near zero
flow) when normal system pressure is attained. When
the pump is in this fully compensated condition, its
internal bypass mechanism provides fluid circulation
through the pump for cooling and lubrication. A relief
valve is installed in the system as a safety backup.
An advantage of the open center system over the
closed center system is that the continuous
pressurization of the system is eliminated. Since the
pressure is built up gradually after the selector valve
is moved to an operating position, there is very little
shock from pressure surges. This action provides a
smoother operation of the actuating mechanisms. The
operation is slower than the closed center system, in
which the pressure is available the moment the
selector valve is positioned. Since most aircraft
applications require instantaneous operation, closed
center systems are the most widely used.
Power systems are designed to produce and
maintain a given pressure. The pressure output of
most of the Navys high-performance aircraft is 3,000
psi. The hydraulic system, shown in figure 7-2, is an
example of a representative 3,000 psi hydraulic power
system. The aircraft has three independent hydraulic
power systems. The two primary systems are the
flight hydraulic power system and the combined
hydraulic power system. These systems are
pressurized by two independent engine-driven
hydraulic pumps on each engine. The auxiliary
power system also operates on 3,000 psi pressure. It
is pressurized by the hydraulic hand pump and/or the
electric motor-driven hydraulic pump. The auxiliary
power system is similar to the combined hydraulic
power system. The primary difference is that the
combined system supplies hydraulic pressure to
utility hydraulic circuits and the flight controls.
The hydraulic control valves and actuators that
operate the primary flight controls are of the tandem
construction type. This design permits operation
from either or both of the two power systems. With
this arrangement, either engine can fail or be shut
down without complete loss of hydraulic power to
either system. The flight system reservoir supplies
fluid to the two engine-driven flight system pumps.
The combined system reservoir supplies fluid to the
two engine-driven combined system pumps and to the
auxiliary hydraulic power system. Both reservoirs
are of the pressurized piston type. They are
pressurized by engine bleed air during engine
operations and by an external air (nitrogen) source
during maintenance operations.
Hydraulic system pressure is indicated on the
integrated hydraulic pressure indicator.
This
indicator displays the output pressure of the flight and
combined hydraulic power systems.
The flight
hydraulic power system provides power for the
operation of the rudder, stabilizer, and flaperons. It
also provides power for operation of the automatic
flight control system actuators, which are an integral
part of the rudder and stabilizer control surface
actuators. The flight hydraulic system also controls
the automatic operation of the isolation valve. This
valve is a part of the combined hydraulic system.
The combined hydraulic power system consists of
two parallel circuitsone to power the primary
systems and the other to power the secondary
systems. The primary system consists of spin
recovery, rudder, stabilizer flaperon, speed brakes,
and electric ram air turbine systems. The secondary
system consists of wing slats, wing flaps, wing fold,
landing gear, arresting gear, wheel brakes, nosewheel
steering, and the nose strut locking systems.
The isolation valve shuts off flow to the
secondary systems during flight and limits the
combined systems pressure requirements to
operation of the primary circuit. Operation of the
isolation valve is both automatic and manual.
The reservoir pressurization system provides the
reservoir with a differential pressure of 40 psi to
prevent engine-driven pump cavitation. The pressure
is maintained at 40 psi by the air regulator. In the
event of regulator failure, the relief valve installed
between the regulator and the reservoir prevents
overpressurization. The relief valve opens at 50 psi.
7-4
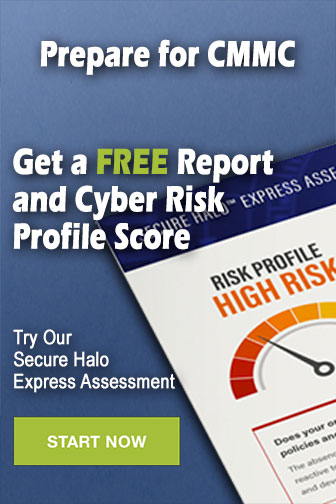